The Surface Of A Mirror Is Flat
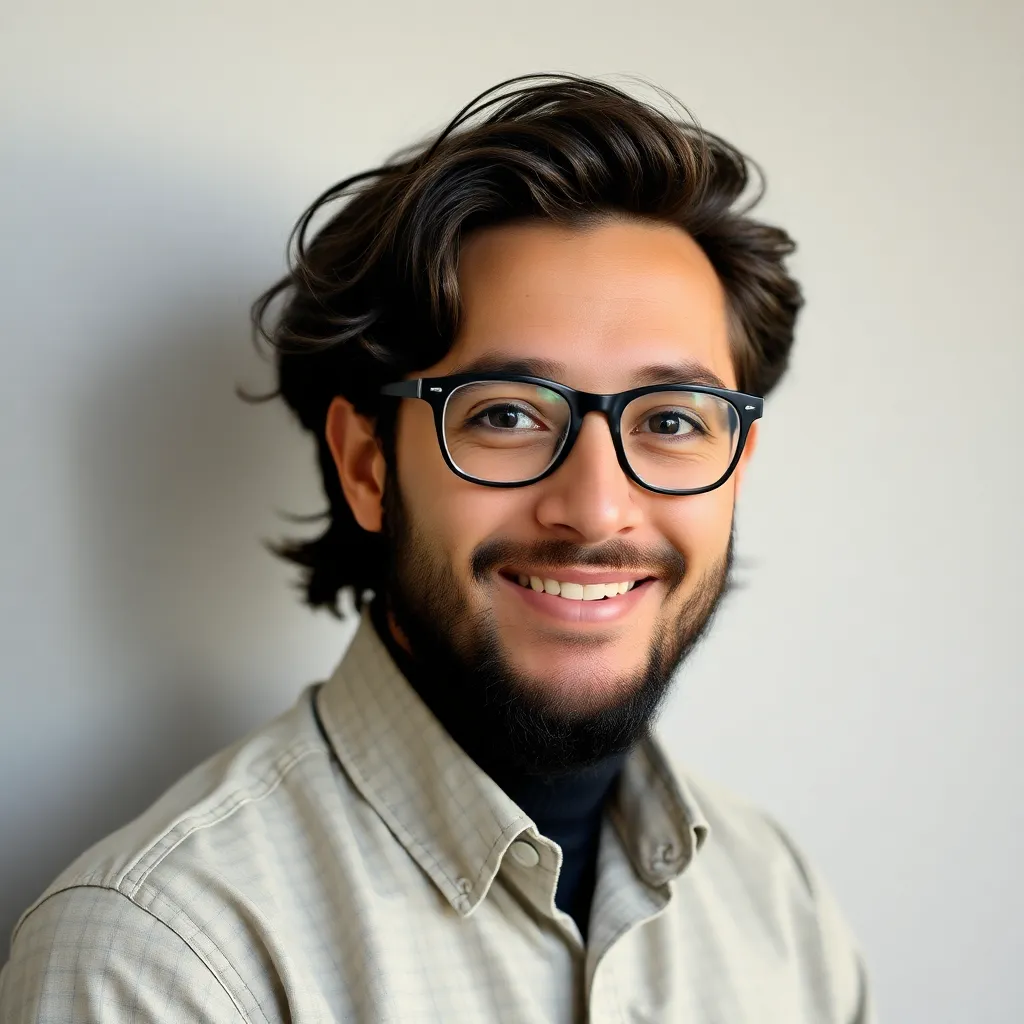
listenit
Apr 05, 2025 · 6 min read
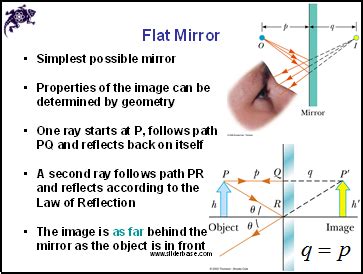
Table of Contents
The Surface of a Mirror: A Deep Dive into Flatness and Reflection
The seemingly simple statement, "the surface of a mirror is flat," belies a fascinating complexity. While intuitively obvious, a closer examination reveals nuanced aspects of surface science, optical physics, and even manufacturing precision that contribute to a mirror's ability to produce a clear and undistorted reflection. This article delves deep into the concept of a mirror's flatness, exploring the scientific principles behind reflection, the practical challenges in achieving true flatness, and the consequences of deviations from ideal flatness.
Understanding Reflection: The Foundation of Mirror Functionality
Before discussing the flatness of a mirror's surface, it's crucial to understand the fundamental principle of reflection. Reflection is the phenomenon where light waves strike a surface and bounce back. The angle at which the light hits the surface (the angle of incidence) is equal to the angle at which it bounces back (the angle of reflection). This is known as the law of reflection, a cornerstone of geometrical optics.
Specular vs. Diffuse Reflection: The Role of Surface Smoothness
The nature of reflection depends heavily on the surface's smoothness. Specular reflection, the type of reflection we associate with mirrors, occurs when light reflects in a uniform and predictable manner from a smooth surface. The reflected rays remain parallel, producing a clear image.
In contrast, diffuse reflection occurs on rough surfaces. Here, light scatters in various directions, preventing the formation of a coherent image. Think of a piece of matte paper; the light reflects diffusely, resulting in a dull appearance rather than a sharp reflection.
A mirror's ability to produce a sharp image hinges on its surface being exceptionally smooth. The microscopic irregularities on the surface must be significantly smaller than the wavelength of visible light (approximately 400-700 nanometers). This ensures that the reflected light waves interfere constructively, resulting in a clear, specular reflection.
Achieving Flatness: The Manufacturing Process of Mirrors
Creating a truly flat mirror surface is a significant technological challenge. The process involves multiple stages, each demanding high precision and control.
Substrate Preparation: The Foundation for Flatness
The foundation of any mirror is its substrate, typically made of glass or other materials like fused silica. The initial stage involves carefully selecting and preparing the substrate material to ensure its inherent flatness. This might involve grinding and polishing the material to a high degree of precision. Even slight imperfections in the substrate can propagate through subsequent stages, affecting the final flatness of the mirror's reflective surface.
Coating Application: Enhancing Reflectivity and Durability
Once the substrate is prepared, a reflective coating is applied. This is often a thin layer of metallic material, such as aluminum or silver, deposited using techniques like vacuum deposition or sputtering. This coating must be uniformly applied to avoid variations in reflectivity across the mirror's surface. The choice of coating material depends on factors like the desired reflectivity, durability, and cost.
Testing and Quality Control: Ensuring Flatness and Performance
Throughout the manufacturing process, rigorous testing and quality control are essential to ensure that the mirror meets its specifications for flatness. Optical interferometry is a common technique used to measure the flatness of a mirror surface with extreme accuracy. This technique uses interference patterns created by light waves reflected from the mirror's surface to detect even minute deviations from flatness.
The acceptable level of deviation from perfect flatness depends on the mirror's intended application. Mirrors for high-precision scientific instruments require significantly higher levels of flatness than those used in everyday household applications. Even small deviations from flatness can lead to distortions in the reflected image, especially in applications requiring high resolution or accuracy.
Consequences of Deviation from Flatness: Distorted Reflections
A deviation from perfect flatness, however small, leads to distortions in the reflected image. These distortions can manifest in several ways:
Aberrations: Introducing Image Distortion
Deviations from perfect flatness cause optical aberrations, which are imperfections in the image formed by a mirror. Common aberrations include:
- Spherical aberration: This occurs when a spherical mirror (not a flat one) doesn't focus light rays perfectly to a single point, resulting in a blurred image. While not directly related to flatness of a flat mirror, it highlights the importance of precise surface shape for optimal imaging.
- Astigmatism: This aberration causes blurring and distortion of the image, especially noticeable in off-axis points. In flat mirrors, slight variations in flatness across the surface can contribute to astigmatic effects.
- Distortion: This manifests as a stretching or compression of the reflected image, altering the shape of objects. Uneven flatness across a mirror's surface directly contributes to distortion.
These aberrations are especially problematic in applications where high image quality is crucial, such as telescopes, microscopes, and laser systems. Even small deviations from flatness can significantly degrade the performance of these instruments.
Wavefront Error: Quantifying Flatness Deviation
The flatness of a mirror's surface is often quantified by its wavefront error. This represents the deviation of the reflected wavefront from a perfectly flat plane. Wavefront error is usually measured in fractions of a wavelength of light. Smaller wavefront errors indicate a higher degree of flatness and improved image quality.
Types of Mirrors and their Flatness Requirements
Different types of mirrors have varying requirements for flatness depending on their application:
Plane Mirrors: Everyday Flatness
Plane mirrors, the most common type, are designed to produce a simple, undistorted reflection. While the level of flatness required for everyday use is relatively low, even minor imperfections can be noticeable in large mirrors or those used in critical applications.
Astronomical Mirrors: Extreme Flatness for Precision
Astronomical mirrors used in telescopes require extremely high levels of flatness. Even tiny deviations can severely impair the telescope's ability to resolve fine details in distant celestial objects. These mirrors undergo incredibly precise manufacturing processes to ensure their flatness is within a fraction of a wavelength of light.
Laser Mirrors: Achieving Perfect Flatness
Laser mirrors require exceptionally high flatness to ensure that the laser beam remains collimated (parallel) and maintains its intensity over long distances. Any deviations from flatness can cause the beam to diverge, reducing its effectiveness.
Beyond Flatness: Other Factors Affecting Reflection
While flatness is paramount, other factors influence a mirror's ability to produce a high-quality reflection:
Surface Cleanliness: Maintaining Optimal Reflection
Even a perfectly flat mirror can produce poor reflections if its surface is dirty or contaminated. Dust, fingerprints, and other contaminants can scatter light, reducing the clarity and brightness of the reflection.
Environmental Conditions: Temperature and Humidity Influence
Temperature and humidity changes can affect the flatness of a mirror, particularly large mirrors. These variations can cause thermal expansion or contraction, leading to slight changes in the mirror's shape and therefore, its reflective properties.
Material Properties: Substrate Choice and Coating
The choice of substrate material and reflective coating significantly impacts the mirror's overall performance. Different materials have different coefficients of thermal expansion and susceptibility to environmental influences.
Conclusion: The Importance of Flatness in Mirror Technology
The seemingly simple concept of a flat mirror surface masks a complex interplay of manufacturing techniques, optical principles, and material science. Achieving true flatness is a significant technological challenge, and the level of flatness required varies dramatically depending on the application. From everyday household mirrors to sophisticated scientific instruments, the precise control of surface flatness is paramount in ensuring the effective functioning of mirrors and the quality of the reflections they produce. The pursuit of perfect flatness continues to drive innovation in material science, optical engineering, and manufacturing precision. Understanding the science behind a mirror's flatness helps us appreciate the ingenuity and precision involved in creating these seemingly commonplace yet remarkably complex objects.
Latest Posts
Latest Posts
-
Common Denominator Of 3 4 5
Apr 05, 2025
-
20 Is What Percent Of 400
Apr 05, 2025
-
How Many Protons Are In A Sulfur Atom
Apr 05, 2025
-
What Is The Square Root Of 2 25
Apr 05, 2025
-
What Is The Least Common Multiple Of 9 And 3
Apr 05, 2025
Related Post
Thank you for visiting our website which covers about The Surface Of A Mirror Is Flat . We hope the information provided has been useful to you. Feel free to contact us if you have any questions or need further assistance. See you next time and don't miss to bookmark.