P 10 P 7 8 9
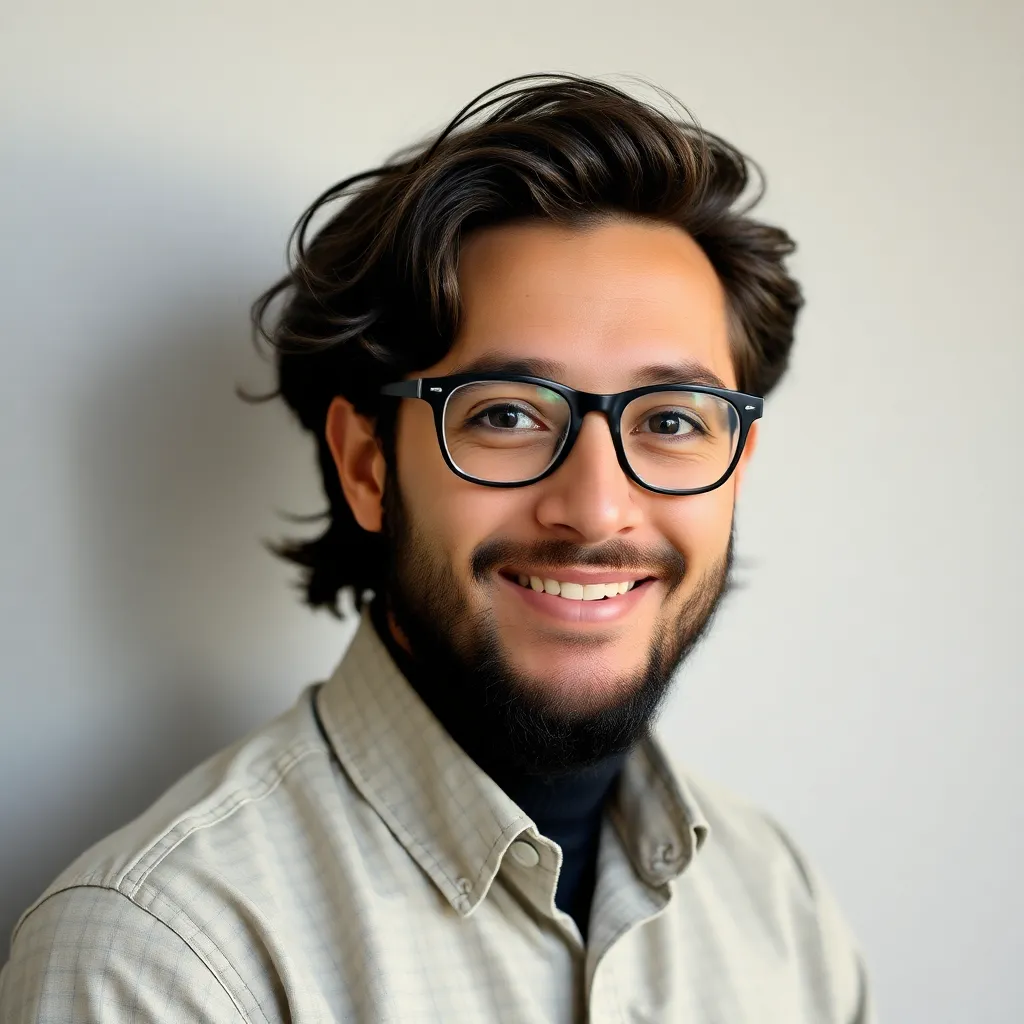
listenit
Mar 15, 2025 · 6 min read
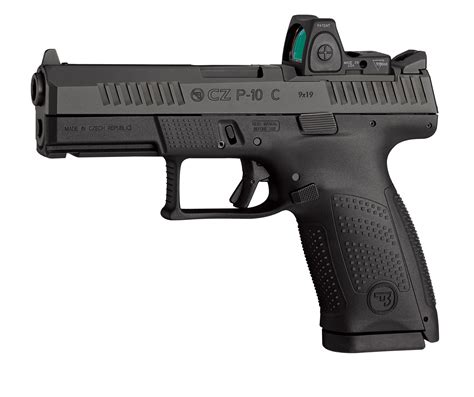
Table of Contents
P-10, P-7, P-8, and P-9: A Deep Dive into the World of Pressure Vessels
The world of industrial manufacturing and processing relies heavily on pressure vessels. These robust containers are designed to hold fluids or gases under pressure significantly higher than the ambient pressure. Understanding the different classes and types of pressure vessels is crucial for ensuring safety, efficiency, and compliance with industry standards. This article delves into the specifics of P-10, P-7, P-8, and P-9 pressure vessels, exploring their design, applications, and the critical considerations for their safe operation. We'll cover construction materials, testing procedures, and the regulations that govern their use.
Understanding Pressure Vessel Classification
Before we dive into the specifics of P-10, P-7, P-8, and P-9, it's essential to grasp the broader context of pressure vessel classification. Pressure vessels are often categorized based on several factors, including:
- Design Pressure: The maximum allowable pressure the vessel can safely withstand.
- Operating Temperature: The temperature range at which the vessel is designed to operate.
- Construction Materials: The materials used in the vessel's fabrication, such as steel, stainless steel, aluminum, or composites.
- Applications: The specific industrial processes or applications where the vessel is used (e.g., chemical processing, oil and gas, power generation).
- Size and Capacity: The physical dimensions and volume of the vessel.
Delving into Specific Pressure Vessel Types: P-10, P-7, P-8, and P-9
While the specific designations P-10, P-7, P-8, and P-9 aren't universally standardized across all pressure vessel codes and standards, these designations often refer to pressure vessels within a specific industry or company's internal classification system. They likely denote different pressure ratings, sizes, materials, or application-specific features. To understand their distinctions, we need to consider the context in which these designations are used.
For a clearer understanding, let's explore the potential interpretations based on common pressure vessel design parameters:
Interpreting "P" Designations:
The "P" prefix might signify "Pressure Vessel" within a particular company or industry code. The numbers following "P" could refer to:
- Pressure Rating: Higher numbers (e.g., P-10) might indicate higher pressure ratings compared to lower numbers (e.g., P-7). This is a common practice in many industrial classifications.
- Size or Capacity: The number might correlate to the vessel's size or liquid/gas capacity. Larger vessels might be designated with higher numbers.
- Material Grade: The number could indirectly reflect the material grade used in construction. Higher grades of steel or other materials often have higher pressure resistance.
- Application-Specific Designations: The numbers could reflect internal company codes related to specific applications or manufacturing processes.
Hypothetical Scenarios and Interpretations
Let's consider some hypothetical scenarios to illustrate how these designations might be understood within a specific context:
Scenario 1: Chemical Processing Plant
In a chemical processing plant, the designations could refer to pressure vessels with varying design pressures:
- P-7: A smaller vessel designed for lower-pressure applications, perhaps holding solvents or other less volatile chemicals. This vessel might be constructed from a standard grade of carbon steel.
- P-8: A medium-sized vessel with a moderate pressure rating. It could be used for reactions under moderate pressures or for storage of moderately volatile chemicals. The material might be a higher grade of carbon steel or stainless steel.
- P-9: A larger vessel designed for higher pressures, potentially handling more reactive chemicals or operating at higher temperatures. Stainless steel or a specialized alloy might be necessary for construction.
- P-10: The largest and highest-pressure vessel in the plant, designed for critical applications, potentially involving hazardous materials. It would require the most robust materials and rigorous safety protocols.
Scenario 2: Oil and Gas Industry
In the oil and gas industry, these designations could reflect different stages in the refining process:
- P-7: A pressure vessel used in early stages of refining, handling low-pressure streams.
- P-8: A vessel used in a later stage of refining, handling higher pressures.
- P-9: A vessel involved in gas processing, handling high-pressure gas streams.
- P-10: A crucial pressure vessel in a critical part of the refinery process that requires exceptional pressure resistance.
Scenario 3: Power Generation
In power generation, these designations could refer to pressure vessels used in different parts of the power cycle:
- P-7: A lower-pressure vessel in the feedwater system.
- P-8: A vessel in the steam generation system operating at moderate pressure.
- P-9: A high-pressure vessel in the steam generation system.
- P-10: A critical component of the system operating at the highest pressure.
Critical Considerations for Pressure Vessel Design and Operation
Regardless of the specific designation (P-10, P-7, P-8, or P-9), the safe design and operation of pressure vessels are paramount. Several critical factors must be considered:
1. Material Selection
The choice of materials is dictated by the operating pressure, temperature, and the nature of the contained fluid. Factors to consider include:
- Yield Strength: The stress at which the material begins to deform permanently.
- Tensile Strength: The maximum stress the material can withstand before fracture.
- Corrosion Resistance: The material's ability to withstand corrosion from the contained fluid.
- Weldability: The ease with which the material can be welded.
Common materials include carbon steel, stainless steel, alloy steels, and non-metallic materials like plastics and composites.
2. Design Calculations
Rigorous engineering calculations are essential to ensure the vessel can withstand the intended pressure and temperature. These calculations typically involve:
- Stress Analysis: Determining the stresses within the vessel walls under various operating conditions.
- Fatigue Analysis: Assessing the potential for fatigue failure due to repeated pressure cycles.
- Creep Analysis: Evaluating the potential for slow deformation under sustained high temperature and pressure.
3. Fabrication and Quality Control
Precise fabrication techniques are critical to ensure the vessel's integrity. This includes:
- Welding: Proper welding techniques are essential to create strong, leak-free joints.
- Non-Destructive Testing (NDT): Techniques like radiographic testing, ultrasonic testing, and magnetic particle testing are used to detect flaws in the welds and base material.
- Pressure Testing: The completed vessel undergoes pressure testing to verify its ability to withstand the design pressure.
4. Safety Devices
Pressure relief devices, such as pressure relief valves and rupture disks, are essential safety features that protect against overpressure.
5. Regular Inspection and Maintenance
Regular inspections and maintenance are crucial to ensure the continued safe operation of pressure vessels. This includes:
- Visual Inspections: Checking for corrosion, leaks, and damage.
- Non-Destructive Testing: Periodic NDT to detect potential flaws.
- Pressure Testing: Periodic pressure tests to verify the vessel's integrity.
Regulatory Compliance
Pressure vessel design, fabrication, and operation are governed by stringent regulations and codes. These codes ensure safety and compliance. Examples include the ASME Boiler and Pressure Vessel Code (BPVC) in the United States and similar codes in other countries. Adherence to these codes is mandatory for ensuring safe operation.
Conclusion
While the specific meanings of P-10, P-7, P-8, and P-9 might vary depending on the context, understanding the broader principles of pressure vessel design, materials, and safety protocols is crucial. The safe operation of pressure vessels is paramount in many industries. Careful attention to design specifications, fabrication techniques, regular inspection, and adherence to safety regulations are essential for preventing accidents and ensuring the longevity of these critical pieces of industrial equipment. This deep dive provides a foundation for understanding the complexities involved in designing, operating, and maintaining these essential components of numerous industrial processes. Always consult relevant codes and standards for your specific application and geographic location to ensure full compliance and optimal safety.
Latest Posts
Latest Posts
-
How To Find The Ph At The Equivalence Point
Mar 15, 2025
-
How Long Would It Take Light To Reach Saturn
Mar 15, 2025
-
How Many Electrons Are In Br
Mar 15, 2025
-
The Elbow Is Blank To The Wrist
Mar 15, 2025
-
How Many Quarts In One Liter
Mar 15, 2025
Related Post
Thank you for visiting our website which covers about P 10 P 7 8 9 . We hope the information provided has been useful to you. Feel free to contact us if you have any questions or need further assistance. See you next time and don't miss to bookmark.