What Is Commutator In Electric Motor
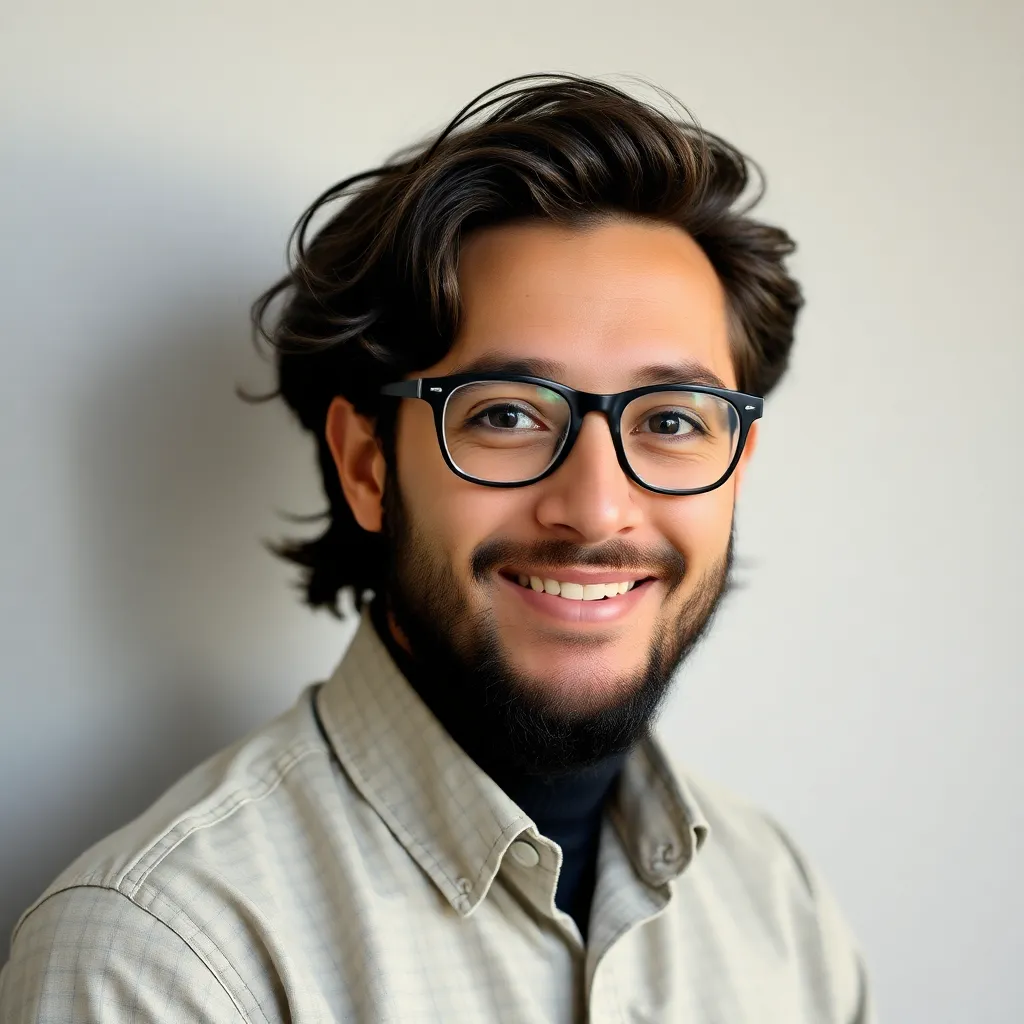
listenit
Apr 23, 2025 · 6 min read

Table of Contents
What is a Commutator in an Electric Motor? A Deep Dive into DC Motor Functionality
The humble commutator. Often overlooked, yet absolutely crucial to the operation of many electric motors, particularly direct current (DC) motors. Understanding its function is key to grasping the mechanics of these ubiquitous machines. This comprehensive guide will delve into the intricacies of the commutator, exploring its construction, working principle, advantages, disadvantages, and its role in the broader context of DC motor technology.
What is a Commutator?
At its core, a commutator is a rotating electrical switch in DC motors. It's a cylindrical component constructed from multiple copper segments insulated from each other, usually by mica. These segments are precisely arranged and connected to the armature windings. The commutator's primary function is to reverse the direction of current flow in the armature windings at precisely the right moments, ensuring continuous unidirectional torque. Without it, a DC motor would simply vibrate and fail to produce rotational motion. Think of it as a mechanical rectifier, transforming the alternating current (AC) induced in the armature into a unidirectional torque.
The Anatomy of a Commutator
The commutator's physical structure is deceptively simple, yet critical for its effectiveness:
-
Copper Segments: These segments are the conductive elements, carefully shaped and insulated to allow for reliable contact with the brushes. The number of segments directly correlates to the number of armature coils.
-
Mica Insulation: High-quality mica, known for its excellent dielectric strength and heat resistance, separates the copper segments. This insulation prevents short circuits between segments, a critical aspect of safe and reliable operation.
-
Commutator Shaft: This cylindrical shaft forms the mechanical backbone of the commutator, providing a strong and stable foundation. It's integral to the motor's overall rotor assembly.
-
Riser: A riser is a small, vertically oriented piece of copper used to connect several commutator segments. This simplifies the internal wiring to the armature windings.
How the Commutator Works in a DC Motor
The commutator's operation is inextricably linked to the motor's magnetic field and armature windings. Here's a breakdown of the process:
-
Magnetic Field Generation: The motor's field magnets (either permanent magnets or electromagnets) create a stationary magnetic field.
-
Armature Current: Current flows from the power source through the brushes, making contact with the commutator segments. This current then flows into the armature windings.
-
Torque Production: The interaction between the current in the armature windings and the magnetic field generates a torque, causing the armature to rotate.
-
Commutation: As the armature rotates, the commutator segments shift their position relative to the brushes. This carefully timed change in contact allows the current to flow through different segments and consequently reverse the current direction in the armature windings.
-
Continuous Rotation: This continuous reversal of current ensures a consistent unidirectional torque, resulting in smooth, continuous rotation. The timing of the commutation is critical – if it’s off, the motor will experience significant vibrations and potential damage.
The Role of Brushes in Commutation
Brushes are carbon-based components that press against the commutator's surface. They provide the essential electrical connection between the power source and the rotating commutator. Their pivotal role is to maintain continuous contact with the moving segments, ensuring uninterrupted current flow. The material selection of brushes is crucial for minimizing friction and wear while maintaining reliable conductivity. The brush pressure must be carefully calibrated; insufficient pressure results in poor contact and sparking, while excessive pressure leads to premature wear.
Advantages of Using a Commutator in DC Motors
Commutators have been a cornerstone of DC motor technology for years, offering several key advantages:
-
Simplicity and Cost-Effectiveness: Compared to other methods of achieving unidirectional torque, the commutator represents a simple and relatively inexpensive solution.
-
High Starting Torque: DC motors with commutators can deliver high starting torque, making them suitable for applications requiring substantial initial force.
-
Speed Control: The speed of a DC motor with a commutator can be easily controlled by adjusting the voltage or current supplied to the armature.
-
Reversability: By simply reversing the polarity of the power supply, the direction of rotation can be reversed.
Disadvantages of Commutators
While commutators offer several benefits, they also present some drawbacks:
-
Mechanical Wear: The constant rubbing action between brushes and the commutator leads to mechanical wear, requiring periodic maintenance and eventual replacement.
-
Sparking: Sparking can occur at the brush-commutator interface, potentially causing radio-frequency interference (RFI) and safety concerns. This is particularly problematic in sensitive electronic environments.
-
Limited Lifetime: The wear and tear on the commutator and brushes inevitably limit the lifespan of the motor.
-
Maintenance Requirements: Regular maintenance, including brush replacement and commutator cleaning, is necessary to ensure optimal performance and prevent failures.
Types of Commutators
While the basic principle remains the same, variations in design and material exist depending on the motor's application and performance requirements:
-
Standard Commutators: These are the most common type, constructed from copper segments and mica insulation.
-
Moulded Commutators: These are formed as a single unit, reducing manufacturing complexities.
-
High-Speed Commutators: These feature specific designs and materials to handle the higher centrifugal forces encountered in high-speed motors.
-
Commutators for High-Current Applications: These are typically constructed with larger copper segments and improved cooling mechanisms to handle the increased current flow.
Commutator Maintenance and Troubleshooting
Regular maintenance is crucial for extending the life and ensuring the reliable operation of a commutator-based DC motor:
-
Brush Inspection and Replacement: Regular inspection of the brushes' wear and length is essential. Worn brushes should be promptly replaced to prevent damage to the commutator and maintain consistent electrical contact.
-
Commutator Cleaning: Accumulated dirt, carbon dust, and other debris can hinder proper electrical contact. Regular cleaning, using appropriate techniques and materials, is crucial for maintaining efficient operation.
-
Surface Inspection: Inspect the commutator's surface for any signs of damage, including uneven wear, grooves, or cracks. Addressing these issues promptly prevents further deterioration.
-
Troubleshooting Sparking: Excessive sparking indicates a problem, such as worn brushes, dirty commutator, or a short circuit in the armature windings. Addressing the root cause is critical to preventing further damage.
The Future of Commutators in DC Motors
While advancements in brushless DC motor technology are increasingly prevalent, commutator-based DC motors still hold a significant place in many applications. Their simplicity, cost-effectiveness, and high starting torque make them attractive options for specific use cases. Ongoing research focuses on improving commutator materials and designs to enhance their longevity, reduce sparking, and improve overall efficiency. However, the trend is towards brushless motors for applications demanding high reliability and reduced maintenance.
Conclusion
The commutator, a seemingly simple component, plays a vital role in the operation of DC motors. Understanding its function, construction, advantages, disadvantages, and maintenance requirements is critical for anyone working with or designing these motors. While brushless motors are gaining ground, the commutator will continue to find its niche in specific applications for the foreseeable future, demonstrating the enduring significance of this ingenious electromechanical device.
Latest Posts
Latest Posts
-
Find The Value Of X That Makes M N
Apr 24, 2025
-
The Density Of Aluminum Is 2 70 G Cm3
Apr 24, 2025
Related Post
Thank you for visiting our website which covers about What Is Commutator In Electric Motor . We hope the information provided has been useful to you. Feel free to contact us if you have any questions or need further assistance. See you next time and don't miss to bookmark.