What Energy Transformation Happens In A Motor
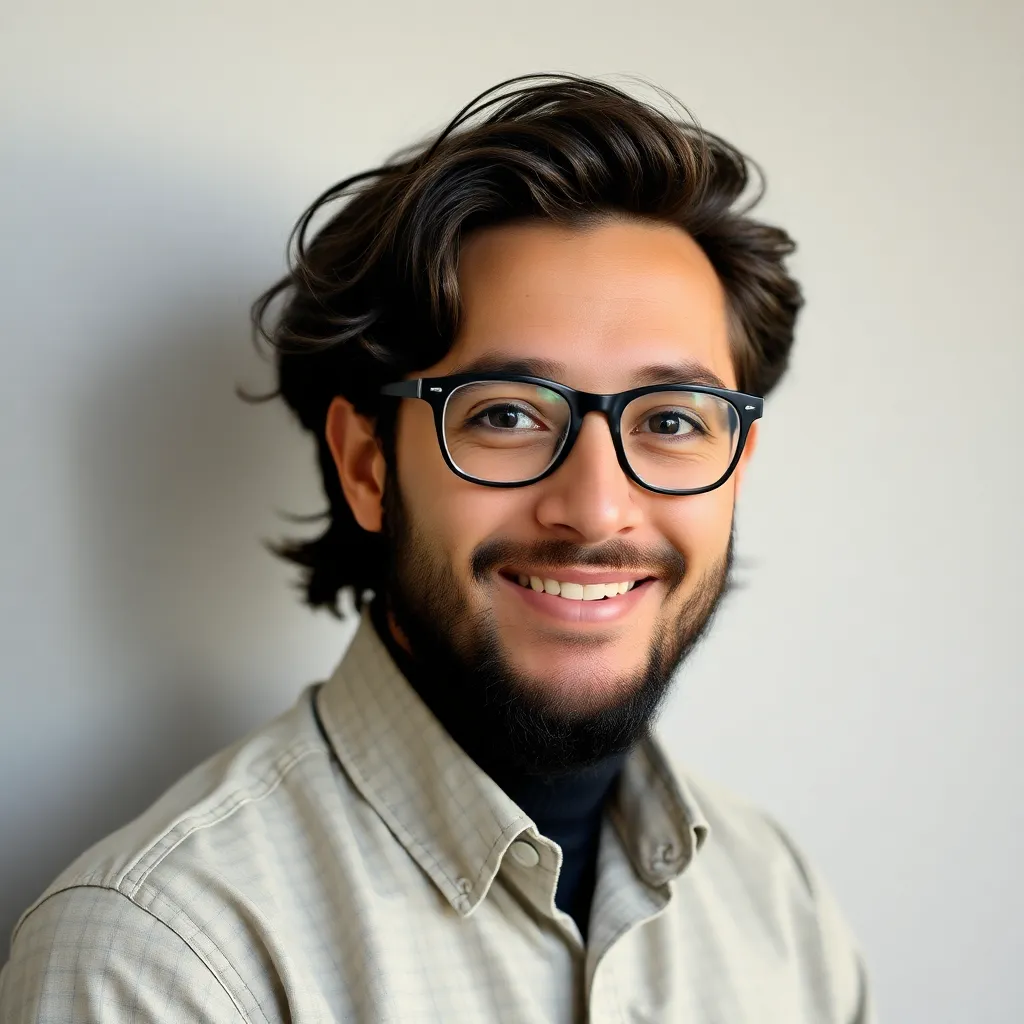
listenit
Mar 16, 2025 · 6 min read
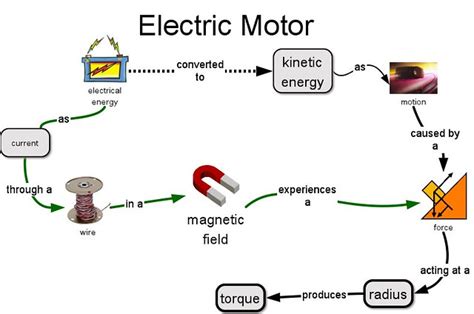
Table of Contents
What Energy Transformations Happen in a Motor?
Electric motors are ubiquitous in modern life, powering everything from our cars and household appliances to industrial machinery and even spacecraft. Understanding the energy transformations within these devices is crucial to appreciating their functionality and efficiency. This article delves deep into the intricate energy conversions that occur within an electric motor, exploring different types of motors and the underlying physics.
From Electrical Energy to Mechanical Energy: The Core Transformation
At its heart, an electric motor's primary function is the conversion of electrical energy into mechanical energy. This seemingly simple process involves a complex interplay of electromagnetic forces and mechanical motion. The precise mechanism of this conversion varies depending on the motor's design, but the fundamental principle remains the same: leveraging the interaction between magnetic fields and electric currents to generate rotational force (torque).
Understanding the Electromagnetic Field
The key to understanding energy transformation in a motor lies in comprehending the electromagnetic field. When an electric current flows through a conductor, it generates a magnetic field around it. This field's strength is directly proportional to the current's magnitude. Conversely, when a conductor moves within an existing magnetic field, an electromotive force (EMF) – a voltage – is induced within the conductor. This principle is fundamental to both electric motors and generators.
The Role of Magnetic Fields and Currents
In a motor, the interaction between these fields and currents drives the rotation. A typical motor contains a stator, the stationary part, and a rotor, the rotating part. The stator typically houses electromagnets or permanent magnets, creating a strong magnetic field. The rotor contains conductors (often coils of wire) that carry electric current.
When current flows through the rotor's conductors, it generates its own magnetic field. The interaction between the stator's magnetic field and the rotor's magnetic field creates a force that causes the rotor to rotate. This force, known as the Lorentz force, is the fundamental mechanism behind motor operation. The direction of rotation is determined by the orientation of the magnetic fields and the direction of current flow (often using Fleming's left-hand rule).
Different Types of Motors and Their Energy Transformations
While the fundamental principle remains the same, the specific energy transformation process varies depending on the motor type. Here's a closer look at some common motor types:
1. Direct Current (DC) Motors
DC motors utilize a direct current supply to generate rotation. These motors often employ a commutator, a segmented ring that reverses the current direction in the rotor's coils as it rotates. This ensures continuous torque and rotational motion. The energy transformation in a DC motor is a relatively straightforward conversion of electrical energy (DC current) into mechanical rotational energy. However, this process is not 100% efficient, and some energy is lost as heat due to resistance in the windings and friction in the bearings.
Types of DC Motors:
- Brushed DC Motors: These use brushes and a commutator to switch the current in the rotor windings, leading to mechanical wear and tear.
- Brushless DC Motors: Employ electronic commutation, eliminating the need for brushes, resulting in increased lifespan and efficiency.
2. Alternating Current (AC) Motors
AC motors operate using an alternating current supply, resulting in a more complex energy transformation process. The varying current creates a fluctuating magnetic field, which interacts with the rotor's magnetic field to produce rotational motion. These motors are widely used due to their robustness and the widespread availability of AC power.
Types of AC Motors:
-
Induction Motors: These are the most common type of AC motor, utilizing electromagnetic induction to create torque. The stator's rotating magnetic field induces currents in the rotor, generating a magnetic field that interacts with the stator's field, causing rotation. The energy transformation here involves the conversion of AC electrical energy into a rotating magnetic field in the stator, which then induces current in the rotor, ultimately generating mechanical rotation. Slip is a key factor in induction motors, representing the difference between the stator's magnetic field speed and the rotor's speed.
-
Synchronous Motors: These motors operate at a constant speed synchronized with the frequency of the AC supply. They require an external source to excite the rotor's magnetic field, often DC current. The energy transformation in a synchronous motor involves the precise alignment of the stator's rotating magnetic field with the rotor's field, leading to a consistent and controlled rotational speed.
-
Stepper Motors: These motors move in discrete steps rather than continuously rotating. They are controlled by precisely timed pulses of electrical energy, causing the rotor to move in specific increments. The energy transformation involves the conversion of discrete electrical pulses into precise angular movements. They find application in precise positioning systems.
3. Servo Motors
Servo motors are a type of closed-loop control system combining a motor (often a DC or AC motor) with a position sensor and control circuitry. This sophisticated arrangement allows for precise control over the motor's position, speed, and torque. The energy transformation is similar to the underlying motor type (DC or AC), but the addition of the control system adds complexity, improving precision and responsiveness. This added layer increases the system's overall energy consumption.
Energy Losses and Efficiency
No motor is perfectly efficient; some energy is always lost during the conversion process. These losses can be categorized as:
-
Copper Losses (I²R Losses): These are caused by the resistance of the motor windings. The heat generated is directly proportional to the square of the current (I²) and the resistance (R).
-
Iron Losses (Core Losses): These losses are due to hysteresis and eddy currents in the motor's core. Hysteresis refers to the energy lost in repeatedly magnetizing and demagnetizing the core material. Eddy currents are circulating currents induced in the core by the changing magnetic field.
-
Mechanical Losses: These losses are due to friction in the bearings and windage (air resistance).
-
Stray Load Losses: These are miscellaneous losses that are difficult to account for precisely.
The efficiency of a motor is the ratio of its mechanical output power to its electrical input power. Higher efficiency motors minimize energy losses, resulting in cost savings and reduced environmental impact. Factors like motor design, materials, and operating conditions significantly influence efficiency.
Advanced Motor Technologies and Future Trends
Continuous research and development are pushing the boundaries of motor technology. Recent advancements include:
-
High-efficiency motors: Employing advanced materials and designs to minimize energy losses.
-
Permanent magnet motors: Utilizing powerful permanent magnets to enhance efficiency and torque density.
-
Electric vehicle (EV) motors: Specialized motors designed for high performance and efficiency in electric vehicles.
-
Smart motors: Integrating sensors and control systems for enhanced monitoring and optimization.
The future of motor technology is likely to see even more efficient, powerful, and intelligent designs, further optimizing the energy transformation process and minimizing environmental impact.
Conclusion
The energy transformation within an electric motor is a fascinating interplay of electromagnetism and mechanics. While the basic principle remains consistent across different motor types, the specifics of the conversion process vary depending on the motor's design and operating principles. Understanding these transformations is vital for improving motor efficiency, designing more sustainable technologies, and harnessing the full potential of electric motors in various applications. Continued innovation in materials, design, and control systems promises even more efficient and powerful motors in the years to come, playing a crucial role in shaping a more sustainable future.
Latest Posts
Latest Posts
-
What Is The Lcm Of 2 And 8
Mar 16, 2025
-
How To Convert Rev Sec To Rad Sec
Mar 16, 2025
-
What Is 65 In Fraction Form
Mar 16, 2025
-
Which Of The Following Atoms Has The Largest Atomic Radius
Mar 16, 2025
-
What Is A Product Of Meiosis
Mar 16, 2025
Related Post
Thank you for visiting our website which covers about What Energy Transformation Happens In A Motor . We hope the information provided has been useful to you. Feel free to contact us if you have any questions or need further assistance. See you next time and don't miss to bookmark.