What Alloy Does Tin Make When Mixed With Copper
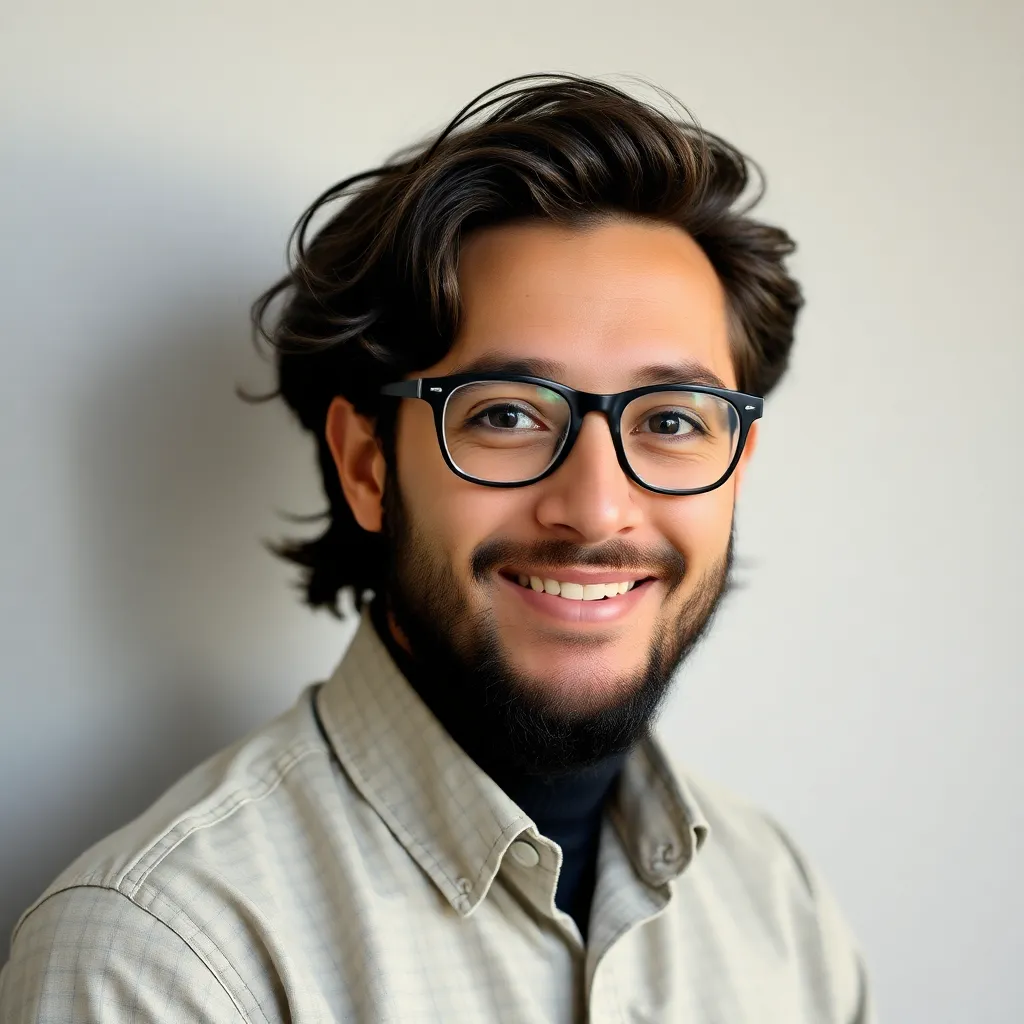
listenit
Apr 25, 2025 · 6 min read

Table of Contents
What Alloy Does Tin Make When Mixed with Copper? Exploring the World of Bronze
The simple answer is bronze. However, the story behind this seemingly straightforward answer is far richer and more complex than one might initially assume. Bronze, an alloy of copper and tin, represents a pivotal point in human history, marking the transition from the Stone Age to the Bronze Age. Its creation and subsequent widespread use profoundly impacted societal development, warfare, art, and technology. This article delves into the fascinating world of bronze, exploring the various alloys created by mixing tin and copper, their properties, applications, and historical significance.
Understanding the Bronze Family: A Spectrum of Alloys
While the general term "bronze" encompasses a wide range of copper-tin alloys, it's crucial to understand that the precise properties of bronze vary significantly depending on the tin content and the presence of other alloying elements. The percentage of tin dramatically influences the resulting alloy's hardness, strength, melting point, and casting characteristics.
The Role of Tin in Copper Alloys
Tin's addition to copper significantly improves its properties. Pure copper is relatively soft and malleable, making it susceptible to deformation. The addition of tin introduces a hardening effect, increasing the alloy's strength and durability. This is due to the formation of intermetallic compounds within the copper matrix, disrupting the regular crystal structure and hindering the movement of dislocations – the microscopic defects responsible for plastic deformation.
The specific properties achieved depend heavily on the tin-to-copper ratio. Alloys with lower tin percentages (typically below 5%) are often referred to as gunmetal and are known for their excellent casting characteristics and relatively good ductility. Higher tin percentages (10-20%) lead to harder and more brittle bronzes, ideal for tools and weapons.
Beyond Tin: The Influence of Other Alloying Elements
The composition of bronze isn't limited to just copper and tin. Throughout history, and in modern metallurgy, other elements have been added to fine-tune the properties of the alloy. These include:
- Zinc: The addition of zinc leads to brass, which is technically not bronze but frequently confused with it. Brass often exhibits superior corrosion resistance than some bronzes. However, bronze and brass were often used alongside one another in manufacturing.
- Lead: Lead improves the fluidity of the molten bronze during casting, resulting in sharper details and easier production of complex shapes. However, it decreases the alloy's strength and corrosion resistance.
- Aluminum: Aluminum additions enhance the strength and corrosion resistance of bronze, finding applications in marine and high-stress applications.
- Manganese: Manganese improves the mechanical properties and wear resistance of bronze, often used in bearings and bushings.
- Silicon: Silicon enhances the fluidity of bronze during casting and improves its mechanical properties.
- Nickel: Nickel increases the strength and corrosion resistance of bronze, particularly in seawater environments.
Exploring Specific Bronze Alloys and their Properties
The vast array of bronze alloys results in a diverse range of properties, tailoring the material for specific applications. Let's delve into some notable examples:
1. Tin Bronze (Standard Bronze):
- Composition: Typically contains 8-12% tin.
- Properties: Exhibits a good balance of strength, hardness, and ductility.
- Applications: Used in bearings, gears, statues, and decorative items.
2. Phosphor Bronze:
- Composition: A tin bronze alloy containing a small percentage of phosphorus (typically 0.01-0.35%).
- Properties: High strength, excellent corrosion resistance, and good wear resistance.
- Applications: Springs, electrical contacts, marine hardware, and musical instruments.
3. Aluminum Bronze:
- Composition: Contains 5-11% aluminum and typically small amounts of other elements such as iron and nickel.
- Properties: High strength, excellent corrosion resistance, and good ductility.
- Applications: High-strength components, marine applications, and structural parts.
4. Silicon Bronze:
- Composition: Contains up to 3% silicon.
- Properties: Improved fluidity during casting and enhanced mechanical properties.
- Applications: Castings, springs, and high-strength components.
5. Manganese Bronze:
- Composition: Typically contains up to 5% manganese.
- Properties: High strength and excellent wear resistance.
- Applications: Propellers, bearings, and other high-stress applications.
The Historical Significance of Bronze
The discovery of bronze marked a watershed moment in human history, ushering in the Bronze Age (approximately 3300-1200 BC). The ability to create stronger, more durable tools and weapons through the combination of copper and tin revolutionized various aspects of life.
Technological Advancements:
Bronze's superior properties compared to stone and copper enabled the development of more efficient tools for agriculture, construction, and warfare. Stronger plows facilitated increased food production, supporting larger and more complex societies. The creation of bronze weapons provided a significant military advantage, leading to shifts in power dynamics and the rise of organized states.
Artistic and Cultural Impact:
Bronze's ability to be cast into intricate shapes allowed for the creation of sophisticated sculptures, ornaments, and other artistic works. The durability of bronze ensured the preservation of these artifacts, providing invaluable insights into ancient cultures and beliefs. Many of the most iconic sculptures and artifacts from ancient civilizations are made of bronze, showcasing the alloy's enduring artistic legacy.
The Bronze Age Collapse:
While the Bronze Age witnessed remarkable advancements, its eventual decline was marked by widespread societal collapse in various parts of the world. Factors contributing to this collapse are complex and debated, but likely involved resource depletion, climate change, and social unrest.
Modern Applications of Bronze Alloys
Despite the passage of millennia, bronze alloys remain relevant in modern technology. Their unique combination of properties makes them indispensable in diverse industries:
- Bearings and Bushings: Bronze's excellent wear resistance and lubricity make it ideal for bearings and bushings in various machinery.
- Marine Hardware: The corrosion resistance of certain bronze alloys makes them crucial for marine hardware, such as propellers, valves, and fittings.
- Springs: Bronze's elasticity and fatigue resistance make it suitable for springs in various applications.
- Electrical Contacts: The conductivity and wear resistance of specific bronze alloys make them suitable for electrical contacts.
- Musical Instruments: Bronze is used in the construction of musical instruments, particularly bells and cymbals.
Conclusion: A Legacy of Innovation
The alloy formed by mixing tin and copper – bronze – is far more than just a metal. It represents a fundamental technological leap in human history, driving societal change and shaping artistic expression for millennia. From its origins in ancient civilizations to its continued use in modern technology, bronze stands as a testament to the power of material science and its profound impact on human progress. The intricate interplay of tin and copper, further refined by the addition of other elements, continues to provide a remarkable range of alloys with unique and valuable properties, ensuring the enduring legacy of this remarkable material. Further research and development in bronze alloys promise to uncover even more exciting applications in the future.
Latest Posts
Latest Posts
-
Converting From Rectangular To Spherical Coordinates
Apr 25, 2025
-
Common Multiples Of 3 4 And 5
Apr 25, 2025
-
14 2 7 Percent As A Fraction
Apr 25, 2025
-
How To Draw An Electron Configuration
Apr 25, 2025
-
None Of These Will Dissolve In Water Lipids
Apr 25, 2025
Related Post
Thank you for visiting our website which covers about What Alloy Does Tin Make When Mixed With Copper . We hope the information provided has been useful to you. Feel free to contact us if you have any questions or need further assistance. See you next time and don't miss to bookmark.