Proportional Limit In Stress Strain Curve
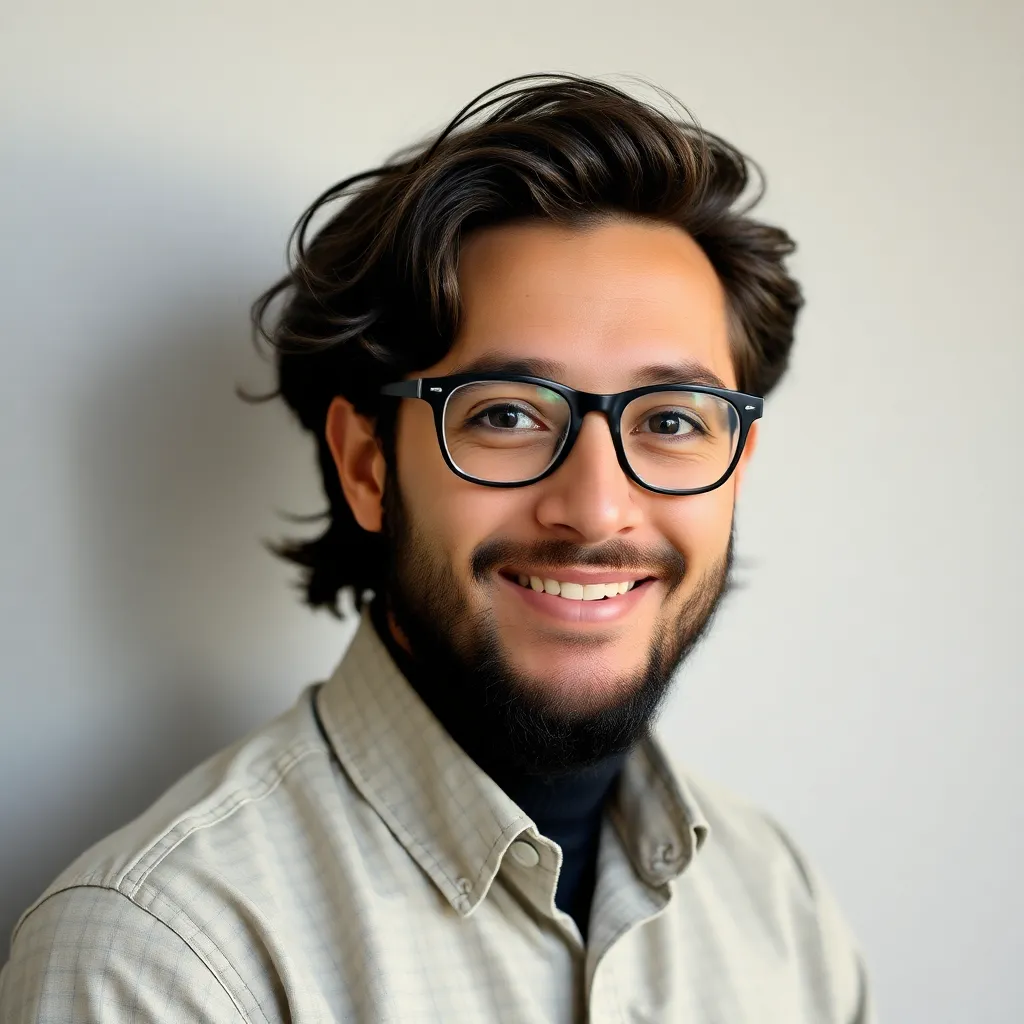
listenit
May 28, 2025 · 7 min read
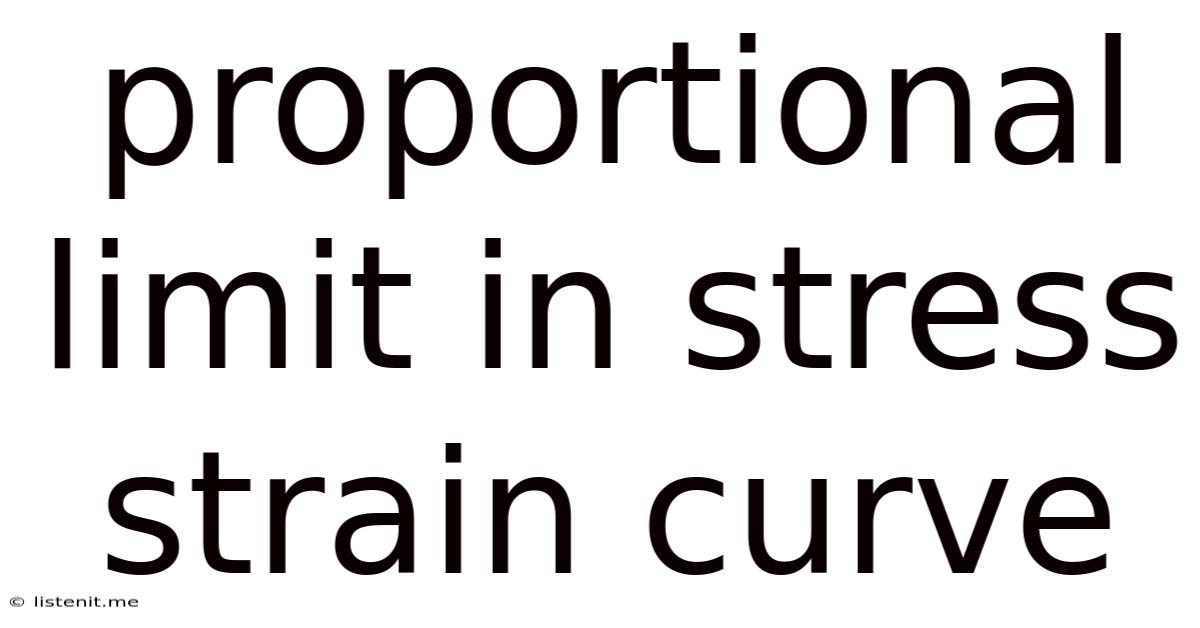
Table of Contents
Understanding the Proportional Limit in the Stress-Strain Curve: A Comprehensive Guide
The stress-strain curve is a fundamental concept in materials science and engineering, providing crucial insights into a material's mechanical behavior under load. A critical point on this curve is the proportional limit, marking the boundary between elastic and plastic deformation. Understanding the proportional limit is essential for engineers in selecting appropriate materials for various applications, ensuring structural integrity, and predicting material failure. This comprehensive guide delves into the intricacies of the proportional limit, exploring its definition, significance, determination, factors influencing it, and its implications in real-world engineering applications.
What is the Proportional Limit?
The proportional limit is the point on the stress-strain curve up to which the stress is directly proportional to the strain. This relationship, known as Hooke's Law, is expressed as:
σ = Eε
where:
- σ represents stress (force per unit area)
- E represents the Young's modulus (a material constant representing stiffness)
- ε represents strain (deformation per unit length)
Below the proportional limit, the material behaves elastically. This means that upon removal of the applied load, the material will return to its original shape and size. The deformation is reversible. Beyond the proportional limit, the relationship between stress and strain becomes non-linear, indicating the onset of plastic deformation. In this region, some permanent deformation remains even after the load is removed.
Distinguishing the Proportional Limit from Other Yield Points
It's crucial to differentiate the proportional limit from other points on the stress-strain curve that define the material's yield behavior, such as the elastic limit and the yield strength. While closely related, these points represent slightly different aspects of material response:
- Proportional Limit: The point beyond which Hooke's Law ceases to hold true. The stress-strain relationship is no longer linear.
- Elastic Limit: The maximum stress a material can withstand without undergoing any permanent deformation. It's often very close to the proportional limit but can be slightly higher.
- Yield Strength: A more practical measure defined as the stress at which a material exhibits a specified amount of permanent deformation (usually 0.2% offset strain). This is commonly used in engineering design as it's easier to determine experimentally than the elastic limit or proportional limit.
The differences between these points can be subtle, and in many materials, they are very close together. However, understanding these subtle distinctions is essential for accurate material characterization and design.
Determining the Proportional Limit
Determining the precise proportional limit experimentally can be challenging due to the subtle transition from elastic to plastic behavior. The following methods are commonly employed:
1. Direct Observation of the Stress-Strain Curve:
The most straightforward approach involves generating a stress-strain curve using a tensile testing machine. The proportional limit is identified as the point of deviation from the initial linear portion of the curve. However, this method requires careful observation and can be subjective.
2. Using the Offset Method:
This method involves drawing a line parallel to the elastic portion of the stress-strain curve, offset by a small strain value (often 0.002 or 0.2%). The intersection of this parallel line with the stress-strain curve is considered an approximation of the yield strength, which is often a reasonable estimate of the proportional limit, especially when the latter is difficult to determine precisely.
3. Extrapolation from the Linear Region:
The initial linear portion of the stress-strain curve can be extrapolated. The point where the extrapolated line intersects the actual stress-strain curve is sometimes considered an approximation of the proportional limit.
Factors Affecting the Proportional Limit
Several factors influence the proportional limit of a material:
1. Material Composition:
The chemical composition of a material significantly impacts its mechanical properties. Alloying elements can strengthen a material and increase its proportional limit. For instance, adding carbon to steel increases its strength and proportional limit. Similarly, the presence of impurities can reduce the proportional limit.
2. Material Structure:
The microstructure of a material plays a critical role in determining its proportional limit. Factors such as grain size, phase distribution, and presence of defects influence the material's ability to resist deformation. Generally, finer grain sizes lead to higher proportional limits.
3. Temperature:
Temperature affects the mechanical properties of materials. Increased temperatures generally reduce the proportional limit, while lower temperatures can increase it. This is because elevated temperatures increase atomic mobility, making dislocation movement easier, thus reducing the resistance to plastic deformation.
4. Strain Rate:
The rate at which a material is deformed (strain rate) also influences the proportional limit. Higher strain rates generally lead to higher proportional limits, as less time is available for dislocation movement.
5. Loading Conditions:
The type of loading (tensile, compressive, shear) influences the measured proportional limit. Materials may exhibit different proportional limits under different loading conditions. Furthermore, the presence of stress concentrations due to geometric features can significantly reduce the apparent proportional limit.
Importance of the Proportional Limit in Engineering Design
Understanding the proportional limit is crucial in various engineering applications:
1. Structural Design:
Engineers must ensure that structural components operate within the elastic region, below the proportional limit, to avoid permanent deformation and potential failure. This is vital in designing bridges, buildings, aircraft, and other structures. Using materials with high proportional limits is essential to achieve the required strength and stiffness.
2. Machine Design:
In machine design, components are subjected to various stresses and strains. Knowing the proportional limit is essential in selecting materials that can withstand these loads without undergoing plastic deformation. This is crucial for maintaining the accuracy and functionality of machines.
3. Material Selection:
Engineers must carefully select materials based on their mechanical properties, including their proportional limit. The choice of material depends on the specific application and the required level of strength and stiffness. Materials with high proportional limits are preferred for applications requiring high strength and durability.
4. Failure Prediction:
The proportional limit serves as an indicator of the material's response to stress. Knowing the proportional limit helps engineers predict material failure under different loading conditions, enabling the development of safer and more reliable structures and machines.
5. Quality Control:
The proportional limit is a key parameter in assessing the quality of materials. Testing materials to determine their proportional limit ensures that materials meet the required specifications and maintain consistency.
Beyond the Proportional Limit: Understanding Plastic Deformation
Once the proportional limit is exceeded, the material enters the plastic region of the stress-strain curve. Plastic deformation is irreversible, leading to permanent changes in the material's shape and dimensions. This region is characterized by several key features:
- Yield Point: The stress at which plastic deformation begins to occur. This is typically marked by a noticeable change in slope on the stress-strain curve.
- Strain Hardening (Work Hardening): As the material undergoes plastic deformation, it becomes stronger and harder. This is reflected in the increasing slope of the stress-strain curve in the plastic region.
- Ultimate Tensile Strength: The maximum stress the material can withstand before necking and eventual fracture.
- Fracture: The point at which the material breaks.
Understanding the plastic deformation behavior is equally vital as understanding the elastic behavior defined by the proportional limit. Many engineering applications deliberately utilize plastic deformation techniques, such as cold working, to enhance material properties.
Conclusion
The proportional limit is a critical parameter in understanding the mechanical behavior of materials. Its determination, though often challenging, is essential for material characterization and engineering design. While the proportional limit marks the transition from elastic to plastic behavior, understanding the entire stress-strain curve—including the plastic region—is essential for comprehending a material's complete mechanical response and for making informed decisions in engineering design and material selection. The factors influencing the proportional limit highlight the complex interplay of material properties and external conditions that govern a material's response to applied loads, emphasizing the need for careful consideration in every application.
Latest Posts
Latest Posts
-
Single Agent Reinforcement Learning With Variable State Space
May 29, 2025
-
Pharmacological Potential Of Illisimonin A An Overview
May 29, 2025
-
Myotonic Dystrophy Type 1 Kinase Drug Targets
May 29, 2025
-
Examples Of Gas Dissolved In Gas
May 29, 2025
-
Hepatic Veins With Minin Phasic Flow
May 29, 2025
Related Post
Thank you for visiting our website which covers about Proportional Limit In Stress Strain Curve . We hope the information provided has been useful to you. Feel free to contact us if you have any questions or need further assistance. See you next time and don't miss to bookmark.