How Does A Hydrostatic Transmission Work
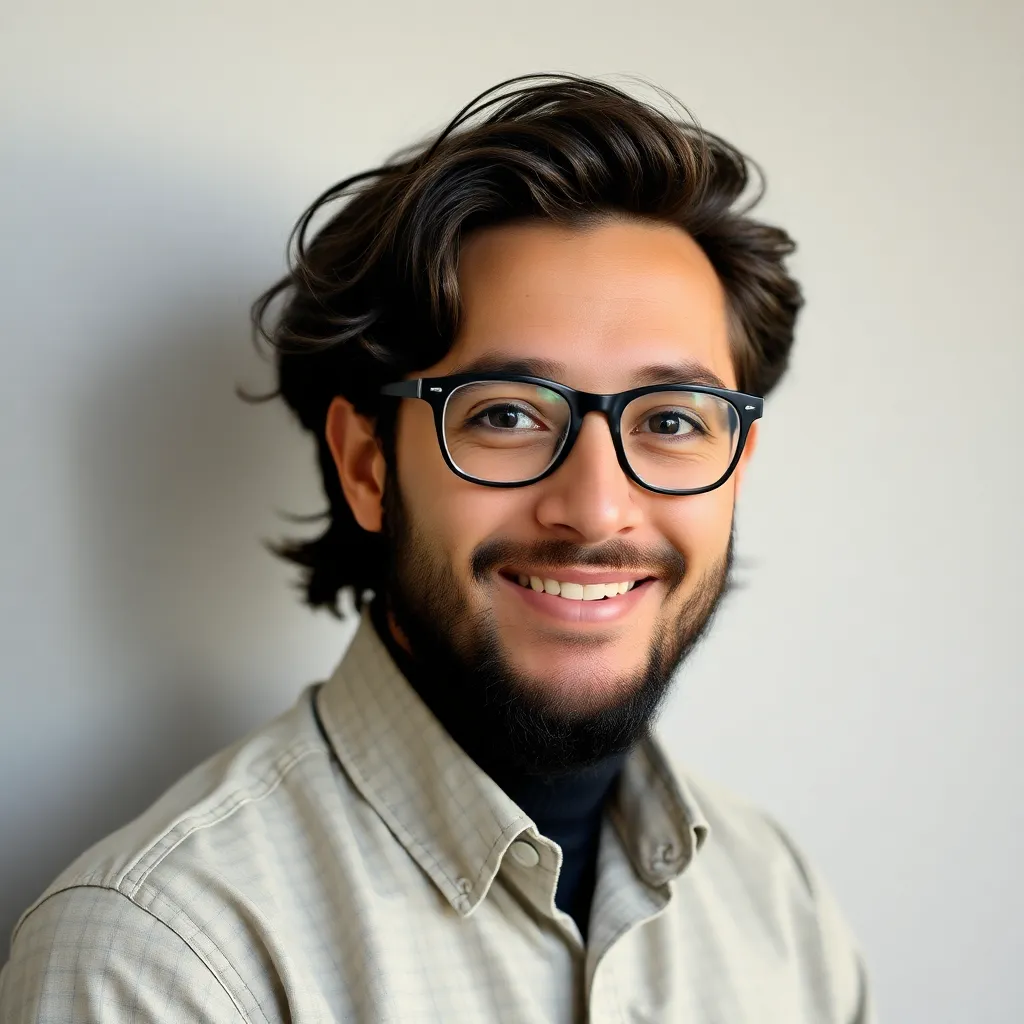
listenit
May 27, 2025 · 7 min read
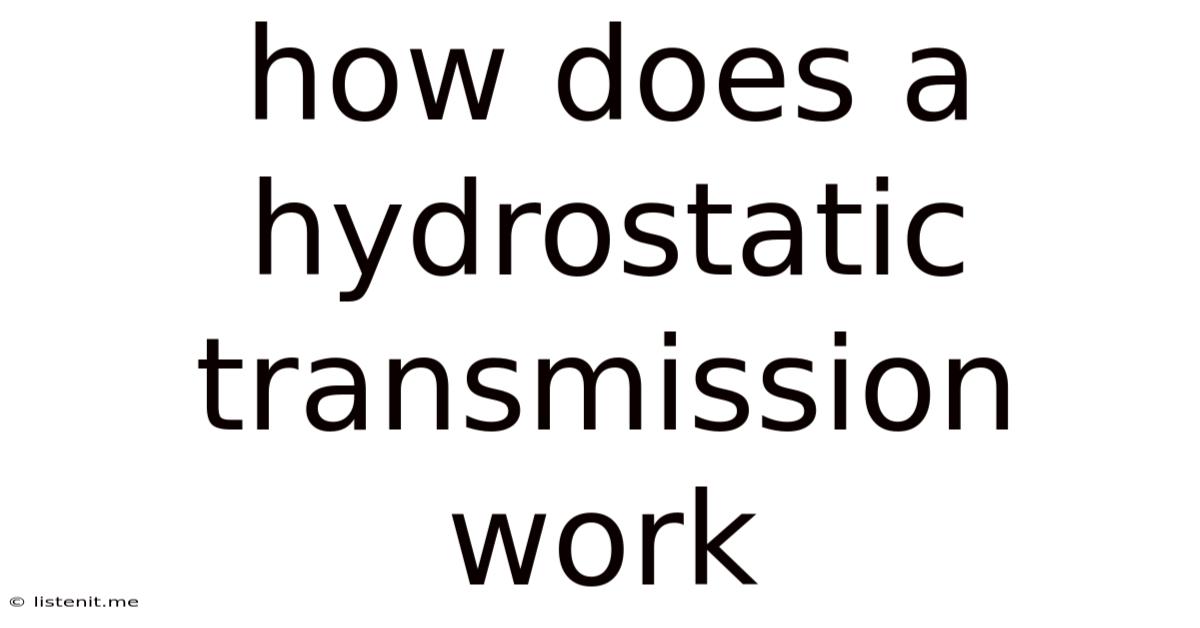
Table of Contents
How Does a Hydrostatic Transmission Work? A Deep Dive into Fluid Power
Hydrostatic transmissions (HSTs) are a marvel of engineering, offering smooth, efficient, and highly controllable power transfer. Unlike traditional gear-based transmissions, HSTs utilize hydraulic fluid to transfer power, providing unparalleled versatility in various applications, from lawnmowers and tractors to industrial machinery and even hybrid vehicles. This article will explore the intricacies of hydrostatic transmissions, explaining their operational principles, advantages, disadvantages, and common applications.
Understanding the Fundamentals of Hydrostatic Transmission
At its core, a hydrostatic transmission relies on Pascal's principle, which states that pressure applied to a confined fluid is transmitted equally in all directions. This principle allows for the efficient transfer of power from a prime mover (typically an engine) to a hydraulic pump, which generates high-pressure fluid. This pressurized fluid then drives a hydraulic motor, converting the hydraulic energy back into mechanical energy to power the output shaft.
The system comprises several key components working in concert:
1. Prime Mover (Engine):
The engine provides the initial mechanical power, which is then converted into hydraulic power. This could be a gasoline engine, diesel engine, electric motor, or even a turbine, depending on the application.
2. Hydraulic Pump:
The heart of the HST, the pump draws fluid from a reservoir and converts the engine's rotational energy into hydraulic energy by increasing the fluid pressure. Different types of pumps exist, including:
- Gear pumps: Simple, reliable, and relatively inexpensive, but less efficient at higher pressures.
- Vane pumps: Offer higher efficiency and pressure capabilities compared to gear pumps.
- Piston pumps: Provide the highest efficiency and pressure, but are more complex and expensive.
The choice of pump depends heavily on the application's specific power and pressure requirements.
3. Control Valve:
The control valve is the brains of the operation, regulating the flow of hydraulic fluid between the pump and the motor. It allows for precise control over the speed and direction of the output shaft. Different types of control valves offer varying levels of sophistication:
- Simple on/off valves: Provide basic control, typically used in simpler applications.
- Proportional valves: Allow for finer control of fluid flow, enabling smoother speed adjustments.
- Servo valves: Offer extremely precise and rapid control, often used in high-performance applications.
The control valve is typically linked to the operator's controls (e.g., pedals, levers), translating the operator's input into adjustments in fluid flow.
4. Hydraulic Motor:
The hydraulic motor receives the high-pressure fluid from the pump, converting the hydraulic energy back into mechanical rotary motion. Similar to pumps, different types of motors exist, each with its own characteristics:
- Gear motors: Simple, reliable, and cost-effective, but less efficient at high speeds.
- Vane motors: Offer improved efficiency and higher speed capabilities compared to gear motors.
- Piston motors: Provide the highest efficiency and power density, ideal for high-performance applications.
The motor's rotational speed is directly proportional to the flow rate of the hydraulic fluid, while the torque is proportional to the pressure.
5. Hydraulic Reservoir:
The reservoir stores the hydraulic fluid, providing a supply for the pump and acting as a heat sink. The fluid needs to be kept clean and at the correct temperature for optimal performance.
How the System Works in Practice: A Step-by-Step Explanation
Let's imagine a simple HST driving a wheel on a piece of machinery:
- Engine starts: The engine powers the hydraulic pump.
- Pump pressurizes fluid: The pump draws hydraulic fluid from the reservoir and increases its pressure.
- Control valve regulates flow: The control valve, based on operator input, directs the pressurized fluid to the hydraulic motor.
- Motor rotates: The hydraulic motor rotates, converting hydraulic energy into mechanical energy.
- Output shaft turns: The motor's output shaft turns the wheel, providing motion.
- Speed and direction control: The control valve modifies the flow rate and direction of the fluid, allowing precise control over the speed and direction of the output shaft (and therefore the wheel). Increasing the flow increases the speed; reversing the flow reverses the direction.
Advantages of Hydrostatic Transmissions
HSTs offer several compelling advantages over traditional gear-based transmissions:
- Infinitely variable speed: HSTs allow for smooth, stepless speed control, without any shifting or jerky movements. This is particularly advantageous in applications requiring precise speed control, such as agricultural equipment.
- High torque at low speeds: HSTs can produce high torque at low speeds, making them ideal for applications requiring high starting torque, such as construction machinery.
- Regenerative braking: In many HST designs, the hydraulic motor can act as a pump, regenerating energy during braking, enhancing efficiency and reducing wear on the braking system.
- Compact size and weight: Compared to gear-based transmissions, HSTs can be more compact and lightweight, freeing up space and reducing overall weight.
- Overload protection: HSTs generally offer inherent overload protection. If the motor encounters excessive resistance, the pressure will increase, but the system will typically protect itself from damage.
Disadvantages of Hydrostatic Transmissions
Despite their advantages, HSTs have some drawbacks:
- Cost: HSTs can be more expensive than traditional gear-based transmissions, particularly for high-power applications.
- Efficiency: While generally efficient, HSTs can experience efficiency losses at higher speeds and under certain operating conditions. The efficiency of the pump and motor components is crucial.
- Leakage: Hydraulic systems are susceptible to leakage, which can lead to fluid loss and reduced performance. Regular maintenance is vital to minimize leakage.
- Fluid contamination: Contamination of the hydraulic fluid can severely impact the performance and longevity of the system. Proper filtration and fluid maintenance are essential.
- Heat generation: HSTs can generate significant heat, especially during prolonged operation under heavy loads. Adequate cooling systems are necessary.
Common Applications of Hydrostatic Transmissions
The versatility of HSTs makes them suitable for a wide range of applications:
- Agricultural machinery: Tractors, combines, harvesters, and other agricultural equipment rely heavily on HSTs for precise speed and torque control.
- Construction equipment: Excavators, loaders, bulldozers, and other construction machinery benefit from the smooth operation and high torque of HSTs.
- Material handling equipment: Forklifts, cranes, and other material handling equipment utilize HSTs for their precise control and maneuverability.
- Industrial machinery: Various industrial machines, such as presses, mills, and conveyors, leverage the advantages of HSTs.
- Mobile equipment: Vehicles like golf carts, airport ground support equipment, and some hybrid vehicles incorporate HSTs.
- Marine applications: HSTs are used in some marine vessels for propulsion and maneuvering.
Maintaining a Hydrostatic Transmission
Proper maintenance is crucial for the longevity and optimal performance of a hydrostatic transmission. This includes:
- Regular fluid level checks: Maintaining the correct fluid level is essential for proper lubrication and cooling.
- Fluid filtration: Regular filter changes are necessary to remove contaminants and prevent damage to system components.
- Fluid quality checks: Periodic checks of the fluid condition (color, clarity) can reveal potential problems.
- Leak checks: Regular inspection for leaks can prevent significant fluid loss and damage.
- Component inspections: Periodic inspection of system components, such as the pump, motor, and valves, can identify potential issues before they become major problems.
Future Trends in Hydrostatic Transmission Technology
Continuous advancements are being made in HST technology, leading to:
- Improved efficiency: Research focuses on developing more efficient pumps and motors, reducing energy loss and improving overall system efficiency.
- Increased power density: Innovations in hydraulic component design allow for greater power output in smaller and lighter packages.
- Enhanced control systems: Advanced control systems provide even more precise and responsive control, optimizing performance across a broader range of operating conditions.
- Integration with other technologies: HSTs are being integrated with other advanced technologies, such as electric motors and regenerative braking systems, to create even more efficient and versatile power transmission solutions.
Conclusion
Hydrostatic transmissions represent a sophisticated and highly effective method for power transfer. Their advantages of smooth, infinitely variable speed control, high torque at low speeds, and inherent overload protection make them invaluable in diverse applications. While there are some drawbacks concerning cost, efficiency at higher speeds, and the need for meticulous maintenance, the benefits of HSTs often outweigh the drawbacks, cementing their position as a vital component in a wide array of machinery and vehicles. Understanding their workings is crucial for anyone working with or maintaining equipment utilizing this powerful and versatile technology.
Latest Posts
Latest Posts
-
The Smear Layer Is Composed Of
May 28, 2025
-
The Sigma Subunit Of Bacterial Rna Polymerase
May 28, 2025
-
How Are Nutrition And Genetics Linked
May 28, 2025
-
Secretion Of Potassium Into The Urine Is
May 28, 2025
-
Where Did The Boer Goat Originate
May 28, 2025
Related Post
Thank you for visiting our website which covers about How Does A Hydrostatic Transmission Work . We hope the information provided has been useful to you. Feel free to contact us if you have any questions or need further assistance. See you next time and don't miss to bookmark.