Fretting Corrosion Is Most Likely To Occur
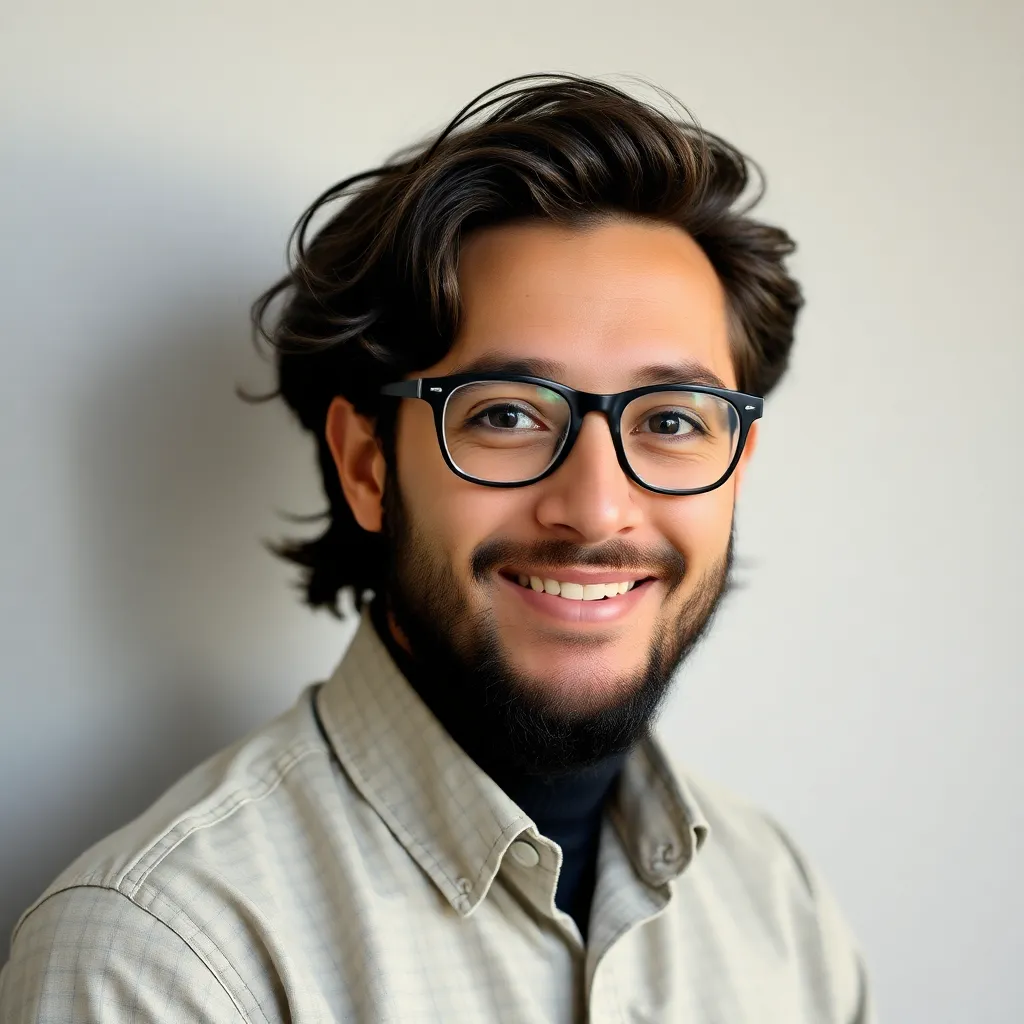
listenit
May 28, 2025 · 6 min read
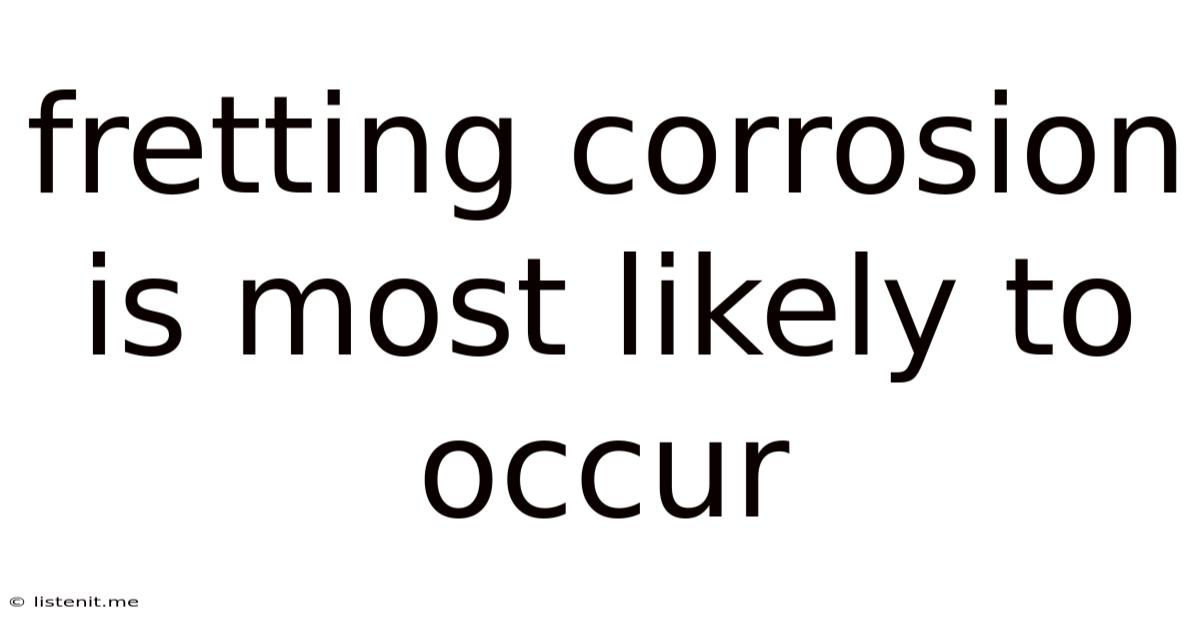
Table of Contents
Fretting Corrosion: Where and Why It's Most Likely to Occur
Fretting corrosion, a sneaky form of material degradation, silently undermines the structural integrity of components in countless applications. Understanding where and why it's most likely to occur is crucial for preventing costly failures and ensuring the longevity of engineered systems. This comprehensive guide delves into the intricacies of fretting corrosion, exploring its causes, influencing factors, and the environments where it thrives.
What is Fretting Corrosion?
Fretting corrosion is a localized form of corrosion that occurs at the interface of two contacting surfaces under small-amplitude oscillatory movement. Unlike regular wear, it's not simply the abrasion of material. Instead, it's a complex interaction between mechanical wear and chemical corrosion. The repetitive micro-movements break down the protective oxide layer on the surfaces, exposing the underlying metal to corrosive attack. This results in the formation of characteristic fretting debris – a fine, powdery mixture of oxides and worn material. This debris can act as an abrasive, further accelerating the corrosion process.
Key Characteristics of Fretting Corrosion:
- Small Amplitude Oscillatory Motion: Movement is crucial; even micrometer-scale oscillations can initiate fretting corrosion.
- High Contact Pressure: Significant contact pressure is required to initiate fretting corrosion.
- Limited Slip: The movement is typically limited; surfaces don't slide freely. This restricted motion concentrates the damage.
- Formation of Fretting Debris: The characteristic powdery debris is a key identifier of fretting corrosion.
- Localized Damage: The damage is concentrated at the contact interface, often leaving surrounding areas unaffected.
Factors Influencing the Occurrence of Fretting Corrosion
Numerous factors contribute to the likelihood and severity of fretting corrosion. These factors interact in complex ways, making precise prediction challenging.
1. Material Properties:
The materials in contact play a significant role. Dissimilar metals are particularly susceptible due to galvanic corrosion, where one metal acts as an anode and corrodes preferentially. Materials with low hardness are more prone to wear and the breakdown of protective oxide layers. The corrosion resistance of the materials is also a critical factor. Materials with inherently poor corrosion resistance are more vulnerable.
2. Environmental Conditions:
The surrounding environment significantly impacts the rate and severity of fretting corrosion. High humidity and the presence of electrolytes (like salt water or acidic solutions) accelerate corrosion. Temperature also plays a role; higher temperatures can increase the rate of chemical reactions. Contaminants such as dust or other particulate matter can exacerbate the problem by acting as abrasives and accelerating wear.
3. Contact Pressure:
The magnitude of the contact pressure is a critical factor. Higher contact pressures generally lead to more severe fretting corrosion due to increased wear and breakdown of the protective oxide layer. However, extremely high pressures can sometimes suppress fretting corrosion by inhibiting relative movement.
4. Amplitude and Frequency of Oscillation:
The amplitude and frequency of the oscillatory movement significantly influence the severity of fretting corrosion. Larger amplitudes and higher frequencies generally lead to more rapid material degradation. The exact relationship, however, can be complex and dependent on other factors.
5. Surface Roughness:
The surface roughness of the contacting surfaces affects fretting corrosion. Rough surfaces tend to have higher contact pressure at asperities, leading to localized stress concentration and enhanced fretting corrosion. Smooth surfaces, while reducing initial wear, can sometimes lead to increased fretting corrosion by creating a tighter contact that hinders the dissipation of fretting debris.
6. Presence of Lubricants:
The use of lubricants can significantly mitigate fretting corrosion. Effective lubricants reduce friction, prevent direct metal-to-metal contact, and help to remove fretting debris. However, the choice of lubricant is crucial, as some lubricants can exacerbate the problem under certain conditions.
Where is Fretting Corrosion Most Likely to Occur?
Fretting corrosion is a pervasive problem affecting a wide range of applications. Its occurrence is often unpredictable, but certain designs and operational conditions are particularly prone.
1. Mechanical Joints:
Bolted joints, riveted joints, and press-fit assemblies are prime locations for fretting corrosion. The oscillatory movement from vibrations, thermal expansion, and load variations creates ideal conditions for fretting. This is particularly true in applications with high-frequency vibrations or fluctuating loads.
2. Rotating Components:
Components experiencing relative motion under pressure, such as shafts, bearings, and gears, are highly susceptible. The repetitive contact between rotating and stationary parts creates the necessary conditions for fretting corrosion. This is particularly critical in high-speed applications or those operating in corrosive environments.
3. Electrical Connectors:
Electrical connectors, especially those subjected to vibration or thermal cycling, are prone to fretting corrosion. The oscillatory motion at the contact interface can disrupt the electrical connection and lead to equipment malfunction or failure.
4. Aerospace Components:
Fretting corrosion is a significant concern in aerospace applications, where components experience high stress, vibration, and potentially corrosive environments. The failure of components due to fretting corrosion can have catastrophic consequences.
5. Medical Implants:
Medical implants, particularly those involving bone-implant interfaces, can experience fretting corrosion. The movement between the implant and bone can lead to corrosion and potential adverse health effects. Careful materials selection and surface treatments are essential to mitigate this risk.
6. Automotive Components:
Automotive components, such as brake systems, engine parts, and suspension components, are frequently affected by fretting corrosion. Vibration, high contact pressure, and sometimes corrosive fluids exacerbate the problem.
Preventing and Mitigating Fretting Corrosion
Preventing fretting corrosion often requires a multifaceted approach combining materials selection, design modifications, and surface treatments.
1. Materials Selection:
Choosing materials with high hardness, good corrosion resistance, and compatibility is crucial. Using similar materials can help reduce galvanic corrosion. Consider materials such as stainless steels, titanium alloys, or specialized coatings designed to resist fretting corrosion.
2. Design Modifications:
Design changes can significantly reduce the likelihood of fretting corrosion. Minimizing contact pressure, avoiding sharp edges and corners, and incorporating features to reduce relative motion can all be effective. Improving surface finish and using proper tolerances to reduce clearance are also critical.
3. Surface Treatments:
Various surface treatments can enhance resistance to fretting corrosion. These include:
- Hard coatings: Coatings like hard chromium or nitriding can increase surface hardness and wear resistance.
- Protective coatings: Coatings like zinc or aluminum can provide corrosion protection.
- Surface texturing: Modifying the surface texture can reduce contact pressure and improve lubrication.
4. Lubrication:
Proper lubrication is a crucial strategy to prevent fretting corrosion. Lubricants reduce friction, separate contacting surfaces, and remove fretting debris. Choosing the right lubricant is critical; the lubricant must be compatible with the materials and the operating conditions.
5. Interference Fits:
Careful control of interference fits can influence fretting. While tight fits may initially appear beneficial, excessive pressure can increase fretting. A well-controlled interference fit balances strength and the minimization of fretting.
Conclusion:
Fretting corrosion, a stealthy enemy of mechanical integrity, demands careful consideration across various engineering disciplines. Understanding its underlying mechanisms and predisposing factors empowers engineers to implement preventative measures effectively. By thoughtfully selecting materials, optimizing designs, employing appropriate surface treatments, and leveraging effective lubrication strategies, the damaging effects of fretting corrosion can be mitigated, ensuring the reliability and longevity of components in diverse applications. Ignoring fretting corrosion can lead to significant financial losses and, in some cases, catastrophic failures. Proactive prevention is not just cost-effective, it's crucial for ensuring safety and reliability.
Latest Posts
Latest Posts
-
Motives And Barriers Related To Phyiscal Activity And Sport
May 29, 2025
-
Limitations That Hinder Nurses From Fully Utilizing Their Skills Geriatric
May 29, 2025
-
Open Heart Surgery Survival Rate By Age 60
May 29, 2025
-
What Is Binary Code In X Ray Physics
May 29, 2025
-
Is There Increased Species Diversty On River Mouths
May 29, 2025
Related Post
Thank you for visiting our website which covers about Fretting Corrosion Is Most Likely To Occur . We hope the information provided has been useful to you. Feel free to contact us if you have any questions or need further assistance. See you next time and don't miss to bookmark.