Finite Elements In Analysis And Design
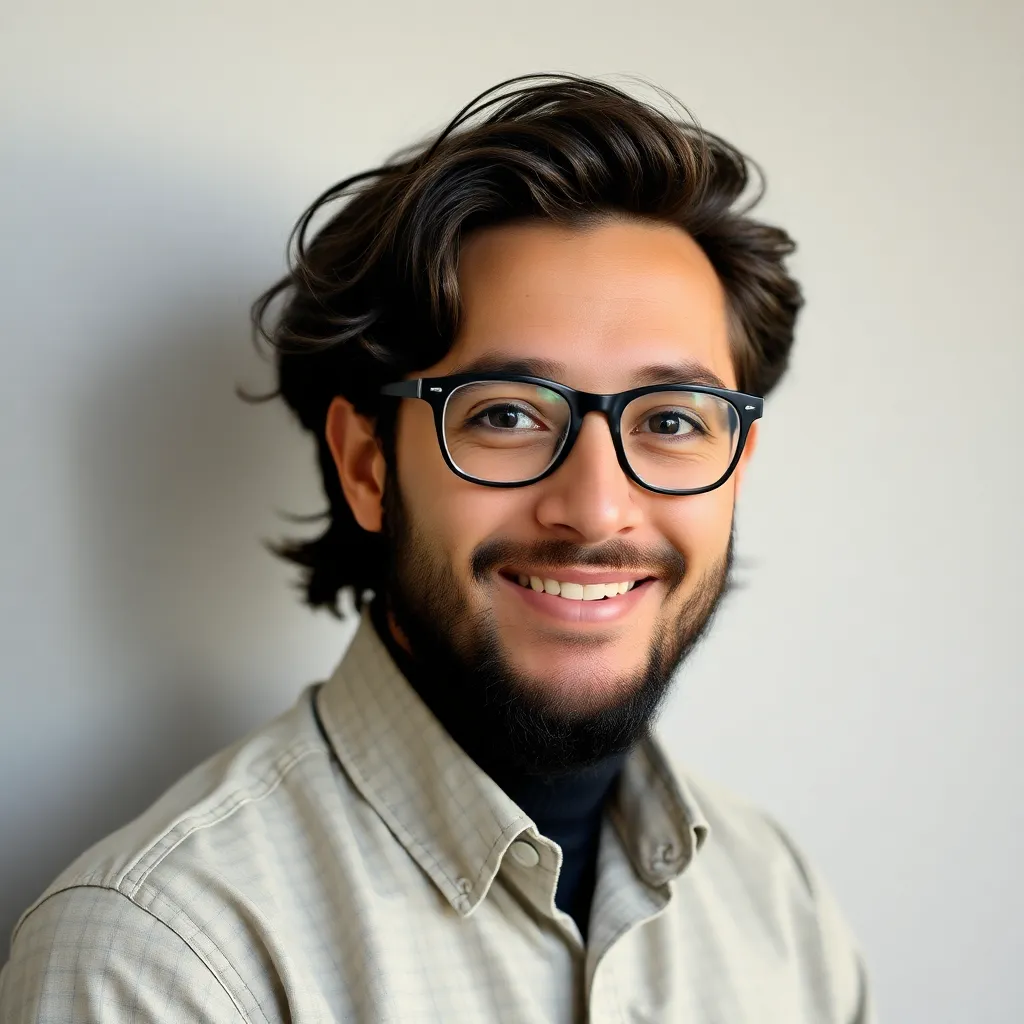
listenit
May 27, 2025 · 6 min read
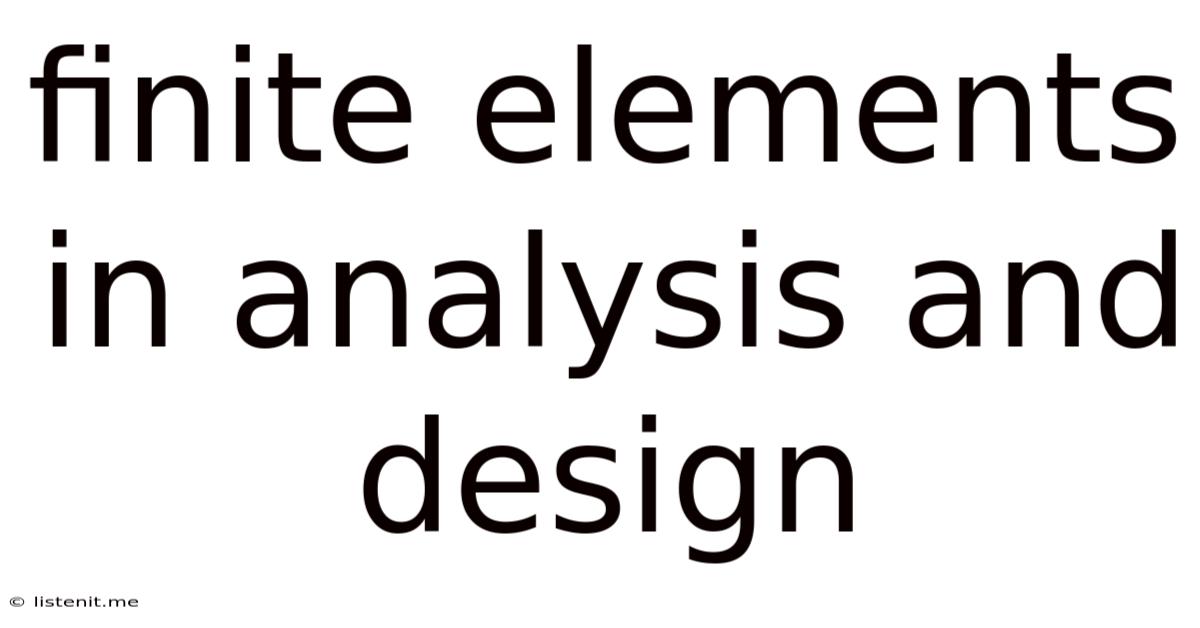
Table of Contents
Finite Elements in Analysis and Design: A Comprehensive Guide
Finite element analysis (FEA) is a powerful computational technique used extensively in engineering and scientific fields for analyzing and designing complex systems. It allows engineers to simulate real-world scenarios, predict component behavior under various loads and conditions, and optimize designs for performance, safety, and cost-effectiveness. This comprehensive guide delves into the core principles, applications, and advantages of finite element analysis in design.
Understanding the Finite Element Method
The finite element method (FEM) is at the heart of FEA. It's a numerical technique that divides a complex structure or system into smaller, simpler elements. These elements are interconnected at nodes, forming a mesh that approximates the original geometry. By analyzing each element individually and assembling the results, the overall behavior of the entire system can be determined.
Key Concepts in FEM:
-
Discretization: The process of dividing a continuous domain (the structure being analyzed) into a finite number of discrete elements. The accuracy of the analysis heavily depends on the mesh quality; finer meshes generally yield more accurate results but increase computational cost.
-
Element Formulation: Each element is assigned material properties and governing equations. These equations, often derived from physical laws (e.g., equilibrium equations in structural mechanics), are simplified and applied to each element. Various element types exist, each suited for specific applications and geometries (e.g., linear, quadratic, tetrahedral, hexahedral).
-
Assembly: The individual element equations are assembled into a global system of equations that represents the entire structure. This involves imposing boundary conditions (constraints on displacements or forces) and solving for the unknown variables (displacements, stresses, etc.).
-
Solution: Solving the global system of equations yields the solution, which describes the behavior of the structure under the applied loads. This often involves advanced numerical techniques like matrix solvers.
-
Post-processing: The results are interpreted and visualized to gain insights into the system's performance. This includes visualizing stress distributions, displacements, and other relevant parameters.
Types of Finite Element Analysis
FEA encompasses a wide range of analysis types, each tailored to specific engineering problems:
1. Static Analysis:
This analyzes structures under static (time-invariant) loads. It determines displacements, stresses, and strains within the structure at equilibrium. Applications include analyzing bridge structures under dead loads, evaluating stress concentrations in mechanical components, and assessing the stability of buildings.
2. Dynamic Analysis:
This analyzes structures subjected to time-varying loads, such as vibrations, shocks, or impacts. It considers inertial effects and determines the structure's dynamic response. Types include modal analysis (determining natural frequencies and mode shapes), transient analysis (analyzing the response over time), and harmonic analysis (analyzing response to sinusoidal loads). Applications include designing earthquake-resistant structures, analyzing the vibration of rotating machinery, and simulating crashworthiness of vehicles.
3. Heat Transfer Analysis:
This simulates the flow of heat through a structure. It determines temperature distributions and heat fluxes under various thermal conditions. Applications include designing efficient heat exchangers, analyzing thermal stresses in electronic components, and optimizing insulation systems.
4. Fluid Flow Analysis (Computational Fluid Dynamics or CFD):
While often considered a separate field, CFD is closely related to FEA and frequently employs similar meshing techniques and solution methods. It analyzes the flow of fluids (liquids and gases), determining pressure, velocity, and temperature distributions. Applications include designing efficient aircraft wings, optimizing pipeline systems, and simulating blood flow in arteries.
5. Non-Linear Analysis:
This addresses situations where material behavior or geometry changes significantly during the loading process. Examples include large deformations, plastic material behavior, or contact problems. Applications include crash simulations, analyzing metal forming processes, and studying the buckling behavior of slender structures.
Advantages of Using FEA in Design
FEA offers numerous advantages over traditional experimental methods:
-
Cost-effectiveness: FEA can significantly reduce the need for expensive physical prototypes and testing, saving time and resources.
-
Improved Design Optimization: FEA allows engineers to rapidly iterate through multiple design options, identifying optimal designs based on performance criteria. This leads to lighter, stronger, and more efficient structures.
-
Enhanced Safety and Reliability: FEA helps identify potential weaknesses and failure modes before a product is manufactured, enhancing safety and reliability.
-
Detailed Analysis: FEA provides detailed insights into stress distributions, displacements, and other critical parameters that are difficult or impossible to obtain through experimental testing.
-
Complex Geometry Handling: FEA can handle complex geometries with ease, enabling accurate analysis of intricate structures.
-
Predictive Capabilities: FEA enables engineers to predict product behavior under various loading conditions, improving design confidence.
Applications of Finite Element Analysis Across Industries
FEA's versatility makes it applicable across a broad spectrum of industries:
-
Aerospace: Analyzing aircraft structures, designing lightweight components, and simulating aerodynamic loads.
-
Automotive: Simulating crashworthiness, optimizing vehicle performance, and analyzing engine components.
-
Biomedical: Modeling human organs, simulating surgical procedures, and designing medical implants.
-
Civil Engineering: Analyzing bridge and building structures, designing foundations, and evaluating seismic response.
-
Manufacturing: Analyzing the stresses and strains during manufacturing processes like casting and forging.
-
Electronics: Designing electronic components that can withstand thermal and mechanical stresses.
Software and Tools for FEA
Several commercial and open-source software packages are available for performing FEA:
- ANSYS: A widely used commercial FEA software package known for its comprehensive capabilities.
- Abaqus: Another leading commercial FEA software with strong capabilities in non-linear analysis.
- Nastran: A widely used FEA solver often embedded within other CAE packages.
- OpenFOAM: A popular open-source CFD software package.
- CalculiX: An open-source FEA solver capable of performing both linear and non-linear analyses.
Challenges and Limitations of FEA
While powerful, FEA has certain limitations:
-
Mesh Dependency: The accuracy of the results depends on the mesh quality. A poorly generated mesh can lead to inaccurate results.
-
Computational Cost: Analyzing large and complex models can be computationally expensive, requiring significant computing resources.
-
Model Simplifications: Real-world structures are highly complex, and simplifications are often necessary when creating the FEA model. These simplifications can affect the accuracy of the results.
-
Material Model Selection: Accurate material models are crucial for obtaining reliable results. Choosing an inappropriate material model can lead to significant errors.
-
Software Expertise: Using FEA software effectively requires significant training and expertise.
Future Trends in Finite Element Analysis
The field of FEA is constantly evolving, with several exciting trends shaping its future:
-
High-Performance Computing (HPC): HPC enables the analysis of increasingly larger and more complex models.
-
Parallel Computing: Breaking down the computational tasks and distributing them across multiple processors reduces computational time.
-
Adaptive Mesh Refinement (AMR): AMR dynamically refines the mesh in regions where high accuracy is needed, improving efficiency.
-
Multiphysics Simulations: Coupling FEA with other simulation techniques, such as CFD and electromagnetic analysis, allows for more comprehensive simulations of complex systems.
-
Machine Learning Integration: Machine learning algorithms can be used to enhance model creation, optimize mesh generation, and improve the accuracy of FEA predictions.
Conclusion
Finite element analysis is an invaluable tool for engineers and scientists involved in the design and analysis of a wide range of products and systems. Its ability to simulate complex scenarios, predict behavior, and optimize designs makes it an essential part of modern engineering practice. By understanding its principles, applications, and limitations, engineers can effectively leverage FEA to create innovative, safe, and efficient designs. The future of FEA promises even more powerful tools and capabilities, further enhancing its impact on various fields.
Latest Posts
Latest Posts
-
Small Ulnar Styloid Avulsion Is Ununited
May 29, 2025
-
Is Low Does Lung Ct Indicated After Negative Pet Ct
May 29, 2025
-
What Causes Abnormal Bone Marrow Signal On Mri
May 29, 2025
-
What Is A Polymer Of Glucose
May 29, 2025
-
Survival Rate With Cribriform Prostate Cancer
May 29, 2025
Related Post
Thank you for visiting our website which covers about Finite Elements In Analysis And Design . We hope the information provided has been useful to you. Feel free to contact us if you have any questions or need further assistance. See you next time and don't miss to bookmark.