Dark A Bands Are Made From
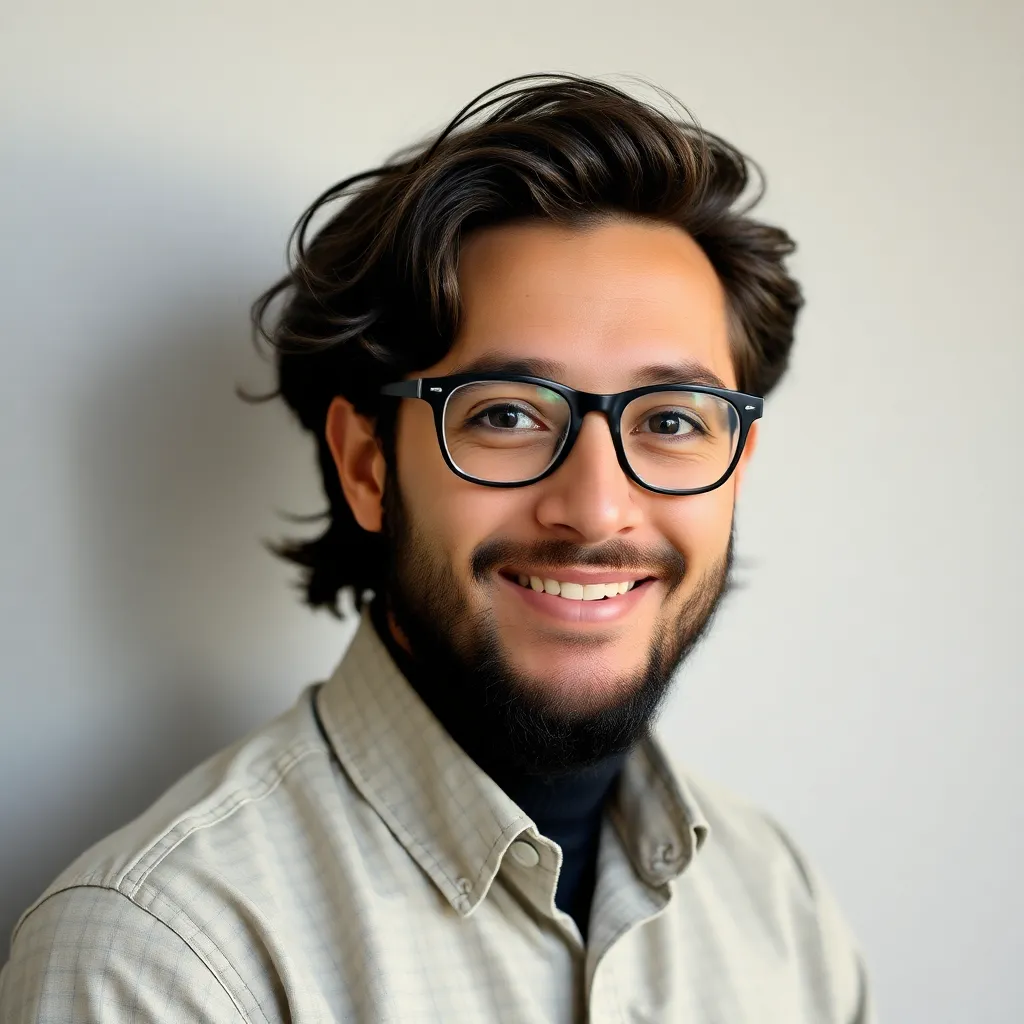
listenit
Apr 22, 2025 · 7 min read

Table of Contents
What Dark Bands Are Made From: A Deep Dive into Materials and Manufacturing
Dark bands, often found in various applications from clothing to industrial settings, aren't simply a single material. Their composition is incredibly diverse, dictated by the intended purpose and desired properties. Understanding what constitutes a "dark band" requires exploring a wide range of materials and manufacturing processes. This comprehensive guide will delve into the different components and techniques used in creating dark bands, covering everything from the raw materials to the final product.
The Spectrum of Dark Band Materials: A Diverse Palette
The term "dark band" is quite broad, encompassing various products with different functionalities and aesthetics. The materials used depend heavily on the intended application. Let's examine some of the key material categories:
1. Textiles and Fabrics: The Woven World of Darkness
Dark-colored bands in textiles are ubiquitous, found in clothing, accessories, and industrial applications. The core materials can include:
-
Natural Fibers: These include cotton, linen, silk, and wool, often dyed with dark pigments to achieve the desired shade. The specific type of fiber influences the band's texture, drape, and durability. For instance, a cotton band will feel different from a silk band, offering varied levels of softness and strength. The dyeing process is crucial here; different dyeing techniques can lead to variations in color depth, fastness, and overall appearance.
-
Synthetic Fibers: Polyester, nylon, acrylic, and rayon are common synthetic choices. These fibers offer advantages such as durability, resistance to shrinking, and easy care. The choice of synthetic fiber affects the band's final properties; nylon is known for its strength, while polyester is often selected for its wrinkle resistance. The pigmentation process for synthetic fabrics often involves solution dyeing, where the color is added to the fiber before it's spun into yarn. This results in exceptionally colorfast fabrics.
-
Blends: Many dark bands utilize blends of natural and synthetic fibers. These blends combine the positive attributes of each type of fiber; for example, a cotton/polyester blend might combine the softness of cotton with the durability and wrinkle resistance of polyester.
2. Rubber and Elastomers: Strength and Flexibility in the Dark
Rubber and elastomers are frequently employed in applications demanding flexibility and durability, often in the form of dark bands:
-
Natural Rubber: Derived from the sap of rubber trees, natural rubber possesses excellent elasticity and tensile strength. However, it's susceptible to degradation from UV light and oxidation, necessitating careful processing and potential additive incorporation.
-
Synthetic Rubber: Materials like styrene-butadiene rubber (SBR), nitrile rubber (NBR), and neoprene offer enhanced properties compared to natural rubber. SBR is a cost-effective option, while NBR excels in oil and chemical resistance. Neoprene, known for its excellent durability and resistance to environmental factors, is a premium choice for demanding applications. These synthetic rubbers are often reinforced with fabrics or other materials to enhance their strength and longevity.
3. Plastics and Polymers: The Versatile Dark Side
Plastics offer a wide array of possibilities for dark bands, providing a vast selection of properties and cost points:
-
Polypropylene (PP): Lightweight, durable, and relatively inexpensive, polypropylene is frequently used in industrial applications. It can be easily pigmented to achieve a range of dark colors and is often used for bands requiring resistance to chemicals or moisture.
-
Polyethylene (PE): Similar to polypropylene, polyethylene is another versatile plastic offering flexibility and resistance to impact. High-density polyethylene (HDPE) is particularly strong and often used in applications where durability is crucial.
-
Polyvinyl Chloride (PVC): PVC is known for its rigidity and durability. Its resistance to chemicals and moisture makes it suitable for applications where exposure to harsh environments is expected. However, it's important to note that PVC production has environmental concerns that need careful consideration.
-
Thermoplastic Elastomers (TPE): These materials combine the properties of plastics and rubbers, offering flexibility, durability, and the ability to be molded into various shapes. TPEs are increasingly used in applications where a balance of flexibility and strength is needed, such as in automotive parts or sporting goods.
4. Metals: Strength and Durability in the Dark
While less common for flexible bands, certain metals can be used to create dark-colored rigid bands:
-
Steel: Steel bands, often galvanized or coated for protection against corrosion, offer exceptional strength and durability. They are commonly used in industrial packaging and construction. Dark-colored steel is often achieved through specialized coatings or through the use of particular steel alloys.
-
Aluminum: Aluminum, despite its lighter weight compared to steel, can also be used for bands requiring high strength and corrosion resistance. Anodizing or powder coating processes can create dark finishes on aluminum bands.
Manufacturing Processes: Shaping the Darkness
The creation of dark bands involves a range of manufacturing processes, depending on the material and the desired outcome:
1. Weaving and Knitting (Textiles): Interlacing Threads of Darkness
For textile bands, weaving and knitting are fundamental processes. Weaving involves interlacing warp and weft yarns at right angles, creating a stable and durable structure. Knitting involves looping yarns together, creating a more flexible and often stretchier fabric. Both techniques can produce dark bands with varying textures and properties.
2. Extrusion (Plastics and Rubbers): Squeezing Out Darkness
Extrusion is a continuous manufacturing process where molten plastic or rubber is pushed through a die, creating a continuous band of the desired shape and dimensions. This process is highly efficient for producing long lengths of dark bands.
3. Injection Molding (Plastics): Shaping Darkness with Precision
Injection molding is used to create more complex shapes and designs. Molten plastic is injected into a mold cavity, where it cools and solidifies into the desired shape. This process is precise and allows for high-volume production of dark bands with intricate details.
4. Casting (Metals and Rubbers): Pouring Darkness into Form
Casting involves pouring molten material into a mold, allowing it to solidify. This method allows for the creation of complex shapes and is suitable for metals and some types of rubber.
5. Braiding (Textiles and other materials): Intertwining strands for strength and flexibility
Braiding involves intertwining several strands of material to create a strong and flexible band. This technique is often used for bands requiring high tensile strength and flexibility, such as those used in lifting or securing applications.
Coloration Techniques: Achieving the Perfect Shade of Dark
Achieving the desired dark color in a band often involves sophisticated coloration techniques:
1. Dyeing (Textiles): Immersing in Darkness
Dyeing involves immersing the fabric in a dye bath to impart color. Different dyeing techniques, such as reactive dyeing, vat dyeing, and direct dyeing, offer varying levels of color fastness and brightness.
2. Pigmentation (Plastics and Rubbers): Incorporating Darkness
Pigments are added directly to the material during the manufacturing process, resulting in a uniformly colored band. The choice of pigment is crucial for achieving the desired shade and ensuring color fastness.
3. Coating (Metals): Layering on Darkness
Coatings, such as powder coating, paint, or anodizing, are applied to the surface of metal bands to provide a dark finish and protection against corrosion.
Applications of Dark Bands: A Wide Range of Uses
Dark bands find applications across numerous industries and sectors:
-
Clothing and Fashion: Dark-colored bands are extensively used in clothing accessories such as belts, straps, and trim.
-
Packaging: Industrial packaging frequently employs dark-colored bands for securing goods during shipping and handling.
-
Automotive: Dark bands are used in various automotive applications, such as seals, gaskets, and trim.
-
Industrial Equipment: Dark bands play a role in industrial machinery, often serving as reinforcing elements or protective coverings.
-
Construction: Dark bands might be used as reinforcement in construction materials or as protective coverings for cables and pipes.
-
Sporting Goods: Dark bands are found in various sporting goods, from wristbands to straps on equipment.
Conclusion: The Complexity of Darkness
The seemingly simple "dark band" is, in reality, a testament to the diverse range of materials and manufacturing techniques available. The choice of material and process is dictated by the intended application, the desired properties, and budgetary constraints. This comprehensive exploration highlights the complexity involved in producing seemingly simple components and underscores the importance of understanding the nuances of material science and manufacturing in diverse industrial contexts. The next time you encounter a dark band, consider the journey it took from raw material to finished product – a testament to human ingenuity and technological advancement.
Latest Posts
Latest Posts
-
To Which Era Do William Shakespeares Plays Belong
Apr 22, 2025
-
How Many Gallons Are In 21 Quarts
Apr 22, 2025
-
A Process That Absorbs Heat Is
Apr 22, 2025
-
Charles Law And Hot Air Balloons
Apr 22, 2025
-
Is N2 An Element Or Compound
Apr 22, 2025
Related Post
Thank you for visiting our website which covers about Dark A Bands Are Made From . We hope the information provided has been useful to you. Feel free to contact us if you have any questions or need further assistance. See you next time and don't miss to bookmark.