Ammonia Separating From N2 And H2
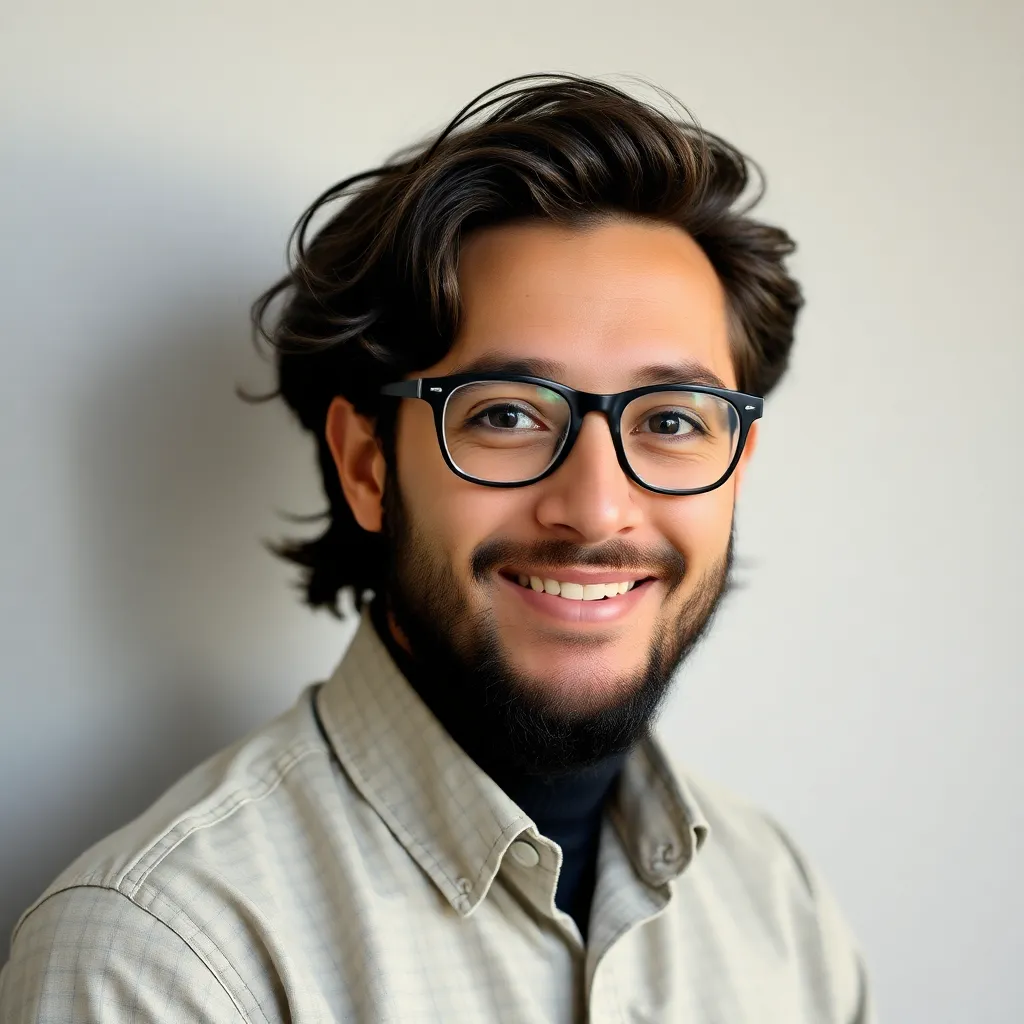
listenit
May 27, 2025 · 5 min read
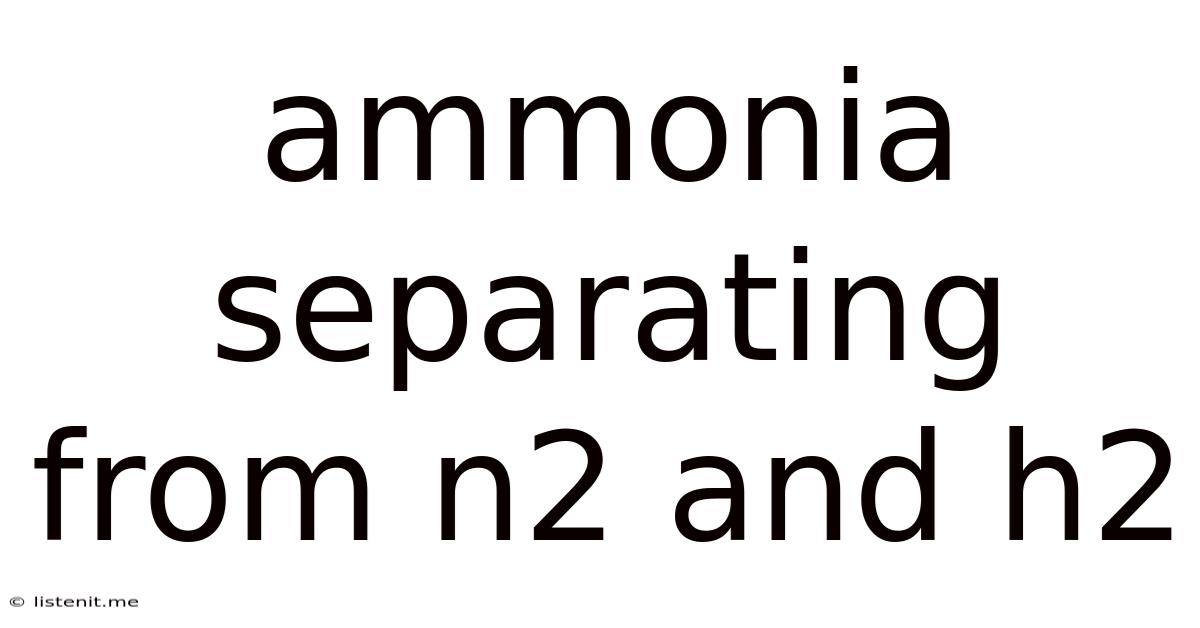
Table of Contents
Ammonia Separation from N2 and H2: A Comprehensive Guide
The Haber-Bosch process, while incredibly efficient at synthesizing ammonia (NH3), produces a gas mixture containing unreacted nitrogen (N2) and hydrogen (H2) in addition to the desired ammonia. Efficiently separating ammonia from this mixture is crucial for maximizing yield, minimizing waste, and ensuring the economic viability of ammonia production. This process is a significant challenge due to the similar physicochemical properties of ammonia, nitrogen, and hydrogen. This article delves into the intricacies of ammonia separation, exploring various techniques, their relative merits, and the ongoing research aiming for even greater efficiency.
Understanding the Challenges of Ammonia Separation
The primary challenge in separating ammonia from a mixture of N2 and H2 lies in the fact that these gases have very similar molecular sizes and boiling points. Traditional separation methods like simple distillation are often ineffective due to the formation of azeotropes – mixtures that boil at a constant composition, making complete separation impossible through simple distillation alone. The close proximity of the boiling points means that high energy input would be needed to achieve separation, making the process expensive and less efficient.
Furthermore, the process needs to be efficient enough to justify the energy consumption. The Haber-Bosch process itself requires significant energy, and any subsequent separation process should be designed to minimize additional energy demands. The separation techniques should also be cost-effective, environmentally friendly, and scalable for large-scale industrial operations.
Key Separation Techniques
Several methods are employed to separate ammonia from the post-synthesis gas mixture. Each method has its strengths and weaknesses, making the selection dependent on specific factors such as scale, desired purity, and economic considerations.
1. Absorption
Absorption utilizes a liquid solvent to selectively dissolve ammonia, leaving behind the relatively insoluble N2 and H2. The solvent absorbs ammonia based on principles of solubility and partial pressure. After absorption, the solvent is then stripped of the ammonia, which is subsequently recovered. This stripping process commonly involves heating the solvent to reduce ammonia solubility. Commonly used solvents include water and various organic solutions.
Advantages:
- Relatively mature technology with established industrial applications.
- Can achieve high separation factors.
Disadvantages:
- Solvent selection is crucial and depends on the operating conditions and purity requirements.
- Solvent regeneration requires energy input.
- Potential for solvent losses and environmental concerns.
- Not ideal for very low concentrations of ammonia.
2. Adsorption
Adsorption uses solid adsorbents with high surface area to selectively bind ammonia molecules. The process relies on the differences in adsorption affinity between ammonia and the other gases. The ammonia-laden adsorbent is then regenerated by changing the pressure or temperature to release the adsorbed ammonia. Zeolites, activated carbon, and metal-organic frameworks (MOFs) are commonly used adsorbents.
Advantages:
- Potentially high efficiency at lower energy consumption compared to distillation.
- Ability to handle lower concentrations of ammonia.
- Potential for use in smaller-scale applications.
Disadvantages:
- Adsorbent selection is critical and dictates the overall effectiveness.
- Adsorbent regeneration can be energy-intensive.
- Adsorbent degradation and lifetime is a concern.
- May require multiple adsorption-desorption cycles for complete separation.
3. Membrane Separation
Membrane separation utilizes selective membranes that allow ammonia to pass through while retaining N2 and H2. This technique is based on the differences in the permeabilities of the gases across the membrane. Polymeric and inorganic membranes are used, with research focused on enhancing selectivity and permeability.
Advantages:
- Energy efficiency potential.
- Compact and potentially scalable design.
- Continuous operation is possible.
Disadvantages:
- Membrane fouling and degradation can limit lifespan.
- Selectivity can be a limiting factor, particularly at high pressures.
- Requires careful membrane material selection.
- High initial investment costs are possible.
4. Cryogenic Distillation
Cryogenic distillation exploits the differences in boiling points between ammonia, nitrogen, and hydrogen at extremely low temperatures. By carefully controlling temperature and pressure, ammonia can be separated from the other gases through fractional distillation.
Advantages:
- Mature technology with proven reliability for high purity separation.
- High efficiency for large-scale production.
Disadvantages:
- Extremely energy-intensive due to the low temperatures required.
- High capital and operating costs.
- Safety concerns related to cryogenic operations.
Advanced Separation Techniques and Future Trends
Research continually pushes the boundaries of ammonia separation, exploring novel methods and improving existing ones. Some promising approaches include:
-
Improved Adsorption Materials: The development of novel adsorbents with enhanced selectivity and capacity for ammonia is a key area of research. MOFs, in particular, are being extensively investigated due to their highly tunable pore structures and surface functionalities.
-
Membrane Technology Advancements: Efforts are focused on creating membranes with higher selectivity and permeability for ammonia, improving overall separation efficiency and reducing energy consumption. This includes the exploration of novel membrane materials and fabrication techniques.
-
Hybrid Processes: Combining different separation techniques, such as adsorption and membrane separation, offers the potential to create more efficient and cost-effective processes. This synergistic approach allows for leveraging the strengths of each individual technique while mitigating their weaknesses.
-
Process Intensification: Minimizing equipment size and energy consumption through process intensification techniques, such as microchannel reactors and intensified distillation columns, is gaining traction. This approach can significantly reduce the footprint and operational costs of ammonia separation.
-
Artificial Intelligence (AI) and Machine Learning (ML): AI and ML are being explored to optimize the control and operation of ammonia separation units. These tools can analyze real-time data to adjust operating parameters, maximizing efficiency and minimizing energy consumption.
Conclusion
Separating ammonia from a mixture of N2 and H2 is a crucial step in the Haber-Bosch process and ammonia production overall. While traditional methods like absorption and cryogenic distillation are widely used, ongoing research and technological advancements continuously refine these methods and explore novel approaches. The drive towards energy efficiency, cost reduction, and environmental sustainability shapes future developments in this vital field. The pursuit of better separation techniques promises not only improved ammonia production efficiency but also significant contributions to a more sustainable and efficient chemical industry. The challenges are substantial, but the potential rewards – a more sustainable and efficient way to produce a crucial chemical – are considerable. The ongoing development and optimization of ammonia separation methods are essential for meeting the growing global demand for ammonia and its numerous applications in agriculture, industry, and energy.
Latest Posts
Latest Posts
-
Tripartite Model Of Anxiety And Depression
May 27, 2025
-
Vitamin B12 And Restless Leg Syndrome
May 27, 2025
-
Can Schizophrenia Be Caused By Head Trauma
May 27, 2025
-
Does Gabapentin Have Sexual Side Effects
May 27, 2025
-
Normal Ascending Aorta Size By Age In Cm
May 27, 2025
Related Post
Thank you for visiting our website which covers about Ammonia Separating From N2 And H2 . We hope the information provided has been useful to you. Feel free to contact us if you have any questions or need further assistance. See you next time and don't miss to bookmark.